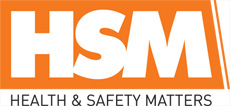
![]() |
Mark Sennett
Managing Editor |
![]() |
Kelly Rose
Editor |
Home> | Industry Update | >Company News | >Lessons learned from the safest Olympics ever |
ARTICLE
Lessons learned from the safest Olympics ever
23 January 2013
Thanks to the emphasis that the Olympic Delivery Authority put on health and safety, the build for the London 2012 Olympic Games has been the safest in history, with not a single death compared with six people constru

Thanks to the emphasis that
the Olympic Delivery
Authority put on health and
safety, the build for the
London 2012 Olympic
Games has been the safest
in history, with not a single
death compared with six
people constructing the last
Olympics in Beijing, and at
least 14 in Athens in 2004.
HSM speaks to the people who made this possible, and finds out what lessons can be learned for the construction industry as a whole
Lawrence Waterman head of health and safety, Olympic Delivery Authority and senior partner, Park Health and Safety Services
The London 2012 work has involved over 45,000 people, hundreds of designers and contractors and over 80m hours worked - so summing up the lessons learned is no easy task. The key however is to look at our major areas of focus: leadership and worker engagement, health as well as safety and good communications.
Leadership The commitment of the ODA as a client was matched by a supply chain of design teams and major contractors determined to do their best for London 2012. But good intentions are not enough, so we established a structure that meant that a Leadership Board at the most senior level led a Leadership Team across the programme involving the project director of each major contractor, and at the local level a Project Leadership Team on each project led by the Tier 1 contractor with representatives of the major subcontractors (Tier 2s and 3s). These weren't talking shops. Decisions made swiftly included: mandatory leadership and communications training for all supervisors, the banning of semiautomatic quick hitches, the "going live" campaign when electrical systems were energised and much much more.
Worker engagement Leadership from the top was vital, but engagement of the people doing the hard work was absolutely essential to make the health and safety programme come to life. Every technique was employed from Daily Activity Briefings for every team to "you said, we did" boards to provide feedback on near miss reports.
Underpinning the general engagement, lots of conversations about safety, was a reward and recognition scheme that ensured we celebrated successes more than we used compliance reviews to identify failures.
Health We demonstrated that you can run health like safety. Preventing ill health through assessing risks in the work and eliminating or managing them, just like accident prevention. Every project team was supported by our modest investment in good advice on how to manage noise, dust, fumes, vibration and the other challenges to health on site. Married with excellent services such as drop-in health centres and campaigns on sexual health, smoking cessation and diet this was a winning formula.
Communications No more poorly drafted and even more poorly designed letters on notice boards.
We used high quality communications material from our marketing team, and spoke to our workforce professionally with excellent posters and leaflets - and even more importantly, we listened including carrying out regular surveys and market research. Our sites were one big conversation on how health and safety could be improved while getting the job done to time and within the budget.
Of course, the best lessons to have been learned are simply stated: There is a fantastic level of skill and knowledge in the construction industry, and when targeted by a knowledgeable client they can be deployed to achieve a brilliant health and safety result Workers are proud to work on a safe project, and very interested in looking after their own health
The 2012 Olympic Park has been the most successful construction delivery of any modern day games. Not only completed on time, within budget and to exceptional quality, but most importantly it is the first Olympics without a fatality. The accident frequency rate was the lowest and productivity the highest. So why was this and what lessons are there to be learned? The client has to provide leadership in setting down the standards to be adopted on the site, the ODA were exemplary in doing this The client must engage all stakeholders at the start of the project including designers, contractors, unions, HSE, and of course workers, and get them to support with their own leadership Proving good health and safety facilities and looking after the wellbeing of your workforce saves you money, it is not a cost We have to get the message over that good health and safety makes commercial sense It is important to encourage reporting of near misses and share route causes.
Client must adopt a procurement process that lays down the standards for H&S and encourages contractors to participate Mandatory medical checks should apply to all workers before starting on site Safety Leadership Teams to be established at all levels to include mamagement and workers,to review and monitor H&S issues All workers to receive a daily site briefing before starting work Assessment process to be put in place to review supervisor competence Every site should have some medical facility available to all workers either on site or a visitng service for smaller sites.
The introduction of this on the Olympic Site has reduced sickness away from work by 70%, and improved productivity immensely Engagement with the work force is essential, use of observation cards to seek their views is helpful.
In order for the construction industry to benefit from the good practice established on the Olympics, Government needs to take a lead by embedding the standards in the procurement process for all their contracts. Industry through its various bodies such as the UKCG should adopt these standards and impose them on their own supply chains. The relevant information on lessons learned from the Olympics is well detailed on the ODA legacy website: learninglegacgy.london2012.com Stephen Williams, director of operational strategy and the London 2012 Games, Health and Safety Executive (HSE) The Health and Safety Executive stated at the outset a commitment to act as an enabling and proportionate regulator for the London 2012 Olympic and Paralympic Games. Our strategy has been based on early intervention coupled with targeted inspection of high risk activities, to ensure that standards are being met.
We worked closely with the Olympic Delivery Authority (ODA) throughout the construction project, setting clear objectives and providing advice and input to ensure that key risks were identified and robust management systems put in place.
The ODA rose to the challenge and demonstrated what can be achieved when there is genuine commitment to high standards of health and safety on the part of the client.
Health and safety was integrated into the project from the start by the ODA through standards and requirements.
Contractors were empowered to develop their own good practice and drive their own health and safety performance. This included a range of worker engagement initiatives designed to foster proper twoway dialogue, underpinned by a 'fair blame' culture which allowed workers to raise issues without the fear of reprisal in an open and transparent manner and participate in solving problems. Strong emphasis was put on the role of supervisors in leading and engaging the workforce.
HSE shared with the ODA an aim to ensure a strong health and safety legacy from the construction project, and cooperated with them on a series of research projects to capture the good practice and lessons learned for future application.
We believe this experience can be used as a catalyst to effect positive change in safety standards across the construction industry. The powerful combination of strong leadership and supply chain engagement is already evident on Crossrail and can be repeated on major projects including HS2 and nuclear newbuild.
HSE will be challenging not only these large clients but also small and medium sized construction companies to prioritise health and safety and aim for the highest standards. Many initiatives adopted on the Olympic construction project were not costly or complicated and are transferable to smaller projects. For instance, daily safety briefings can be done whether you have two or 200 people on site.
Strong, active leadership of health and safety at all levels together with effective worker engagement and clear standards for all on site, including the supply chain, can be put in place on all sites.
In addition to the research evidence on the positive impact of effective health and safety strategies and techniques, there is a wealth of practical case study material that can be taken 'off the shelf' and applied to future construction projects.
And finally there are the many contractors and thousands of construction workers who have been involved in the Olympic project, and who can share their experience. Their actions and expectations will be particularly influential in helping the construction industry to build on the improvements already achieved and raise safety standards across the board.
For more information, visit: www.hse.gov.uk/aboutus/london-2012- games/lessons-for-industry.htm
HSM speaks to the people who made this possible, and finds out what lessons can be learned for the construction industry as a whole
Lawrence Waterman head of health and safety, Olympic Delivery Authority and senior partner, Park Health and Safety Services
The London 2012 work has involved over 45,000 people, hundreds of designers and contractors and over 80m hours worked - so summing up the lessons learned is no easy task. The key however is to look at our major areas of focus: leadership and worker engagement, health as well as safety and good communications.
Leadership The commitment of the ODA as a client was matched by a supply chain of design teams and major contractors determined to do their best for London 2012. But good intentions are not enough, so we established a structure that meant that a Leadership Board at the most senior level led a Leadership Team across the programme involving the project director of each major contractor, and at the local level a Project Leadership Team on each project led by the Tier 1 contractor with representatives of the major subcontractors (Tier 2s and 3s). These weren't talking shops. Decisions made swiftly included: mandatory leadership and communications training for all supervisors, the banning of semiautomatic quick hitches, the "going live" campaign when electrical systems were energised and much much more.
Worker engagement Leadership from the top was vital, but engagement of the people doing the hard work was absolutely essential to make the health and safety programme come to life. Every technique was employed from Daily Activity Briefings for every team to "you said, we did" boards to provide feedback on near miss reports.
Underpinning the general engagement, lots of conversations about safety, was a reward and recognition scheme that ensured we celebrated successes more than we used compliance reviews to identify failures.
Health We demonstrated that you can run health like safety. Preventing ill health through assessing risks in the work and eliminating or managing them, just like accident prevention. Every project team was supported by our modest investment in good advice on how to manage noise, dust, fumes, vibration and the other challenges to health on site. Married with excellent services such as drop-in health centres and campaigns on sexual health, smoking cessation and diet this was a winning formula.
Communications No more poorly drafted and even more poorly designed letters on notice boards.
We used high quality communications material from our marketing team, and spoke to our workforce professionally with excellent posters and leaflets - and even more importantly, we listened including carrying out regular surveys and market research. Our sites were one big conversation on how health and safety could be improved while getting the job done to time and within the budget.
Of course, the best lessons to have been learned are simply stated: There is a fantastic level of skill and knowledge in the construction industry, and when targeted by a knowledgeable client they can be deployed to achieve a brilliant health and safety result Workers are proud to work on a safe project, and very interested in looking after their own health
The 2012 Olympic Park has been the most successful construction delivery of any modern day games. Not only completed on time, within budget and to exceptional quality, but most importantly it is the first Olympics without a fatality. The accident frequency rate was the lowest and productivity the highest. So why was this and what lessons are there to be learned? The client has to provide leadership in setting down the standards to be adopted on the site, the ODA were exemplary in doing this The client must engage all stakeholders at the start of the project including designers, contractors, unions, HSE, and of course workers, and get them to support with their own leadership Proving good health and safety facilities and looking after the wellbeing of your workforce saves you money, it is not a cost We have to get the message over that good health and safety makes commercial sense It is important to encourage reporting of near misses and share route causes.
Client must adopt a procurement process that lays down the standards for H&S and encourages contractors to participate Mandatory medical checks should apply to all workers before starting on site Safety Leadership Teams to be established at all levels to include mamagement and workers,to review and monitor H&S issues All workers to receive a daily site briefing before starting work Assessment process to be put in place to review supervisor competence Every site should have some medical facility available to all workers either on site or a visitng service for smaller sites.
The introduction of this on the Olympic Site has reduced sickness away from work by 70%, and improved productivity immensely Engagement with the work force is essential, use of observation cards to seek their views is helpful.
In order for the construction industry to benefit from the good practice established on the Olympics, Government needs to take a lead by embedding the standards in the procurement process for all their contracts. Industry through its various bodies such as the UKCG should adopt these standards and impose them on their own supply chains. The relevant information on lessons learned from the Olympics is well detailed on the ODA legacy website: learninglegacgy.london2012.com Stephen Williams, director of operational strategy and the London 2012 Games, Health and Safety Executive (HSE) The Health and Safety Executive stated at the outset a commitment to act as an enabling and proportionate regulator for the London 2012 Olympic and Paralympic Games. Our strategy has been based on early intervention coupled with targeted inspection of high risk activities, to ensure that standards are being met.
We worked closely with the Olympic Delivery Authority (ODA) throughout the construction project, setting clear objectives and providing advice and input to ensure that key risks were identified and robust management systems put in place.
The ODA rose to the challenge and demonstrated what can be achieved when there is genuine commitment to high standards of health and safety on the part of the client.
Health and safety was integrated into the project from the start by the ODA through standards and requirements.
Contractors were empowered to develop their own good practice and drive their own health and safety performance. This included a range of worker engagement initiatives designed to foster proper twoway dialogue, underpinned by a 'fair blame' culture which allowed workers to raise issues without the fear of reprisal in an open and transparent manner and participate in solving problems. Strong emphasis was put on the role of supervisors in leading and engaging the workforce.
HSE shared with the ODA an aim to ensure a strong health and safety legacy from the construction project, and cooperated with them on a series of research projects to capture the good practice and lessons learned for future application.
We believe this experience can be used as a catalyst to effect positive change in safety standards across the construction industry. The powerful combination of strong leadership and supply chain engagement is already evident on Crossrail and can be repeated on major projects including HS2 and nuclear newbuild.
HSE will be challenging not only these large clients but also small and medium sized construction companies to prioritise health and safety and aim for the highest standards. Many initiatives adopted on the Olympic construction project were not costly or complicated and are transferable to smaller projects. For instance, daily safety briefings can be done whether you have two or 200 people on site.
Strong, active leadership of health and safety at all levels together with effective worker engagement and clear standards for all on site, including the supply chain, can be put in place on all sites.
In addition to the research evidence on the positive impact of effective health and safety strategies and techniques, there is a wealth of practical case study material that can be taken 'off the shelf' and applied to future construction projects.
And finally there are the many contractors and thousands of construction workers who have been involved in the Olympic project, and who can share their experience. Their actions and expectations will be particularly influential in helping the construction industry to build on the improvements already achieved and raise safety standards across the board.
For more information, visit: www.hse.gov.uk/aboutus/london-2012- games/lessons-for-industry.htm
MORE FROM THIS COMPANY
- Workers at risk as 33% of SMEs experienced accidents in the past year
- South Essex College students lead the way
- 44% of workers say winter has negative effect on their mental wellbeing
- Five tips to help keep skin safe in the sun
- Parliamentarians join call for CO safety on boats following report into Lake Windermere deaths
- Workplace absence costs UK economy £18bn per year
- The Health & Safety at Work Act at 40 and beyond
- New initiative aims for occupational health step change
- Employers’ spying on staff 'reaches a new low in work relations'
- UK sickness absence costing £23.5bn a year
OTHER ARTICLES IN THIS SECTION