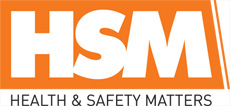
![]() |
Mark Sennett
Managing Editor |
![]() |
Kelly Rose
Editor |
1/7 (1 to 10 of 69)
Break the fall | 06/02/2020 |
---|---|
Despite years of advancements in occupational health, falls are still the most common type of injury experienced by workers. Add height into the equation, and you increase the risk of fatality or life-long care. Dr Karen McDonnell looks at the prevention strategy campaigns and the stories behind the statistics. THE UK is one of the safest places to work in the world, it is consistently one of the lowest rates of fatal injury across the European Union [1]. But the annual injury statistics show people are still having what I call “old” accidents, leading to types of injury that, despite decades of advancement in occupational safety in prevention, were being suffered by workers in the first of half of the 20th century. In 2018/19, 40 workers died due to a fall from height. This is up by five from 2017/18, and above the average (36) for the period 2014/15-2018/19 [2]. Falls from height consistently account for the most deaths to British workers, and on top of this, the cost of people falling from height over the past five years is estimated at around £800million, with many people needing lifelong care [3]. At RoSPA, our guiding principle is that accidents don’t have to happen, and this is perhaps no truer than in the workplace. Falls have always been the most common type of injury experienced by the country’s workforce. But despite this common knowledge, and years of experience, training and legislation, it is a challenge that employers are consistently not meeting. For example, in January GB Industrial Cladding Ltd of Doncaster was fined £10,000 after pleading guilty to breaching Working at Height Regulations after a worker fell from a ladder and shattered his elbow. The ladder was being used as access to a roof, and was resting against wet metal wall cladding without being tied or footed. And in the same month, Formation Construction Limited of London was fined £300,000 after admitting breaches of the Health and Safety at Work Act. An employee was using a concrete breaker to make an opening for a stairwell at a site in Acton, when he fell 7.5 metres. Unfortunately, in this instance, the worker suffered fatal head injuries. Following the prosecution, an HSE inspector said the company had identified control measures that could have prevented the fall, but that those safeguards were “virtually absent”. Part of what the inspector said should strike a chord with all of those working to protect workers from falls – that this was a “wholly avoidable incident”. Outside of the workplace, falls are also one of the biggest causes of fatal accidents or a trip to an emergency department. Falls from height is an issue that needs to be tackled, and is something that RoSPA has been working on very recently with The Ladder Association, the membership body for those organisations that require elements of working at height in the UK. Recently, we partnered up on the Get a Grip national ladder safety campaign, promoting the safe use of ladders both at work and at home. Storytelling At the heart of any safety campaign is storytelling, as from experience we know how powerful and effective this method of delivering messages can be. Bombarding your workforce with statistics and safety information will always have limited effect. A more potent means of changing attitudes and behaviour are when safety issues are connected to the emotive and personal. Jason Anker, a friend of RoSPA and someone we work very closely with on this issue, is passionate about telling his own story to ensure that he prevents falls from height. In 1993, when he was 24-years-old, he fell 10ft from a ladder while working on a roof. In doing so, he fractured his back and became paralysed from the waist down. The ladder wasn’t secured and the conditions on the ground were not good. Jason is now living with the consequences of the decision he made that day to climb the ladder. Jason now works as a motivational and behavioural change speaker, giving talks to companies about his experience. The feedback we hear from the places he’s visited always describes the impact he’s had on staff, and how their attitudes towards their own safety are positively affected. Quite often, as a safety training and education organisation, we interact with larger companies that are willing and able to implement proper policies and practices, however, we recognised that we really needed to start reaching those sole traders or small to medium enterprises with a handful of staff – where time really is money, and corners might be cut. The 'Get a Grip' campaign aims to do exactly that, by going one step beyond Jason’s story and telling that of his daughter, Abbi, and the impact his fall had on her and her the rest of the family. Utilising an emotional video, Abbi speaks of her experience growing up with a paralysed father (he had his fall when she was aged just three), and how in later life he was not able to walk her down the aisle or dance with her at her wedding. Jason cannot pick up and play with his granddaughter. In a blog, she also recalls how he couldn’t do the things a normal dad could do, like take her swimming, play soccer or teach them to ride a bicycle. While we’ve been promoting the video and blogs to key stakeholders, her story was also reproduced on a pocket-sized, downloadable leaflet – at last count, since the campaign was launched in the spring, it has had more than 9,000 downloads, so we know the value people are placing in her testimony. Taking messages home Working at height is an issue that there are increasing moves to address here in the UK. Aside from 'Get a Grip', our RoSPA Awards Excellence Forum sees organisations from across the world are sharing what works well to drive up workplace standards, and we saw the creation of the All Party Parliamentary Group for Working at Height, a cross-party group of Members of Parliament dedicated to investigating the topic, which is supported by the Prefabricated Access Suppliers’ and Manufacturers’ Association (PASMA) and the Access Industry Forum. It held a wide-ranging inquiry and consultation into working at height, and why people are still dying from falls, and in April 2019 launched a resulting report which has been presented to the Government and makes a number of recommendations for both employers and regulators. A dedicated charity called the No Falls Foundation launched, with the aims of providing education, research and support for those who have suffered a fall and their families. There are great strides being taken in tackling this issue head-on in workplaces, but the great thing about the 'Get a Grip' campaign is that personal stories will always get to those hard-to-reach places mentioned above, and beyond that, will make people think about what they are doing in their day-to-day home lives too. The vast majority of falls and other unintentional injuries occur in the home or leisure environments, away from the workplace, so as employers we need to ensure we are engendering in our staff behaviour which they will carry over the threshold into the outside world. While we can be guilty of leaving good health and safety practice behind when we clock out every day, stories such as those from Abbi and Jason will literally “hit home”; they won’t be forgotten in a hurry, meaning we will be thinking about them whether we’re welding at 30ft, or doing DIY at home while at the top of an 8ft ladder. When we recognise that our people are at the heart of organisational sustainability, we need to ensure that our health and safety messages are carried by them wherever they are, so we can address the huge burden – not to mention impact on the bottom line – that home-based unintentional injury can create. While the UK has experienced a huge amount of success in saving lives and preventing injuries in the workplace and on the roads throughout the past decades, the number of deaths and serious injuries from accidents is actually on the rise thanks to increases in incidents in home and leisure environments. Coincidentally, a major proportion of these incidents are falls, especially for the older population. As part of RoSPA’s national accident prevention strategy, we are calling on businesses to “carry over” safety programmes from the workplace into other parts of life. This is happening in some places, such as with L’Oreal’s Safe@Work, Safe@Home initiative, but there is so much good practice happening in workplaces across the UK that we know it can be utilised to help reduce the wider societal burden of accidents – we just need to tease it out. If you think you can help us meet this aim, take a look at www.rospa.com/national-strategy. Stories really help us to put people first. They are what lies behind the statistics, the reason for our policies, and most importantly they help people to understand and react. I would urge all health and safety managers dealing with working at height issues (and even those who aren’t) to take a look at Abbi’s story. Her video can be seen at www.ladderassociation.org.uk/get-a-grip, or her blog at www.rospa.com/abbi. OSH managers can also read Jason’s story at www.rospa.com/jason. For those wanting to see the All Party Parliamentary Group’s recommendations into solving the problem of falls from height in the workplace, see www.workingatheight.info. Dr Karen McDonnell is occupational safety and health adviser for Royal Society for the Prevention of Accidents (RoSPA). For more information, visit www.rospa.com References [1] www.hse.gov.uk/statistics/european/european-comparisons.pdf [2] www.hse.gov.uk/statistics/pdf/fatalinjuries.pdf [3] Health & Safety Executive - Costs to Britain of workplace fatalities and self-reported injuries and ill health, 2016/17 |
|
|
|
Dangerous driving | 11/03/2019 |
The most dangerous activity people do at work is driving so managing occupational road risk needs to be a key priority for companies, says Adam Grinsell. Driving is the most dangerous work activity that most people do. Police accident data shows that every year almost one-third of road deaths in the UK – more than 500 people – are killed in collisions involving motorists who are driving for work. On top of that, there are a further 5,000 who are seriously injured, and 40,000 who are slightly injured. This includes other road users, as well as the at-work drivers. Few organisations can operate without using the road network and as a consequence, occupational road risk is likely to be their biggest safety issue. And yet, organisations have been slow to recognise this and driving for work is still being treated as the poor cousin of occupational health and safety. Road crashes during the course of work, even minor ones, are a major cause of loss and a threat to corporate morale and reputation. All employers have duties of care to their staff and the people that they interact with, and thus need to manage this risk within the overall framework that they should have in place for managing health and safety generally (policies, organisation, procedures). Outside of the moral and bottom-line reasons to properly manage this issue, there are very real and stark legal implications too. The HSE’s Driving at Work guidelines stat that “health and safety law applies to on-the-road work activities, and the risks should be effectively manages within a health and safety system” And while the majority of road safety law applies to drivers as individuals and their behaviour, various road traffic acts and regulations also require employers to ensure that vehicles used for work purposes are safe and legal to be on the road, and that drivers are properly licensed and insured. Employers can be held accountable for various “cause or permit” road traffic offences, such as causing or permitting someone to use a handheld mobile while at the wheel, use a vehicle in a dangerous condition, or drive on the road without a valid licence or insurance. Whether large or small, organisations need to have a systematic way of assessing and eliminating or controlling the risks caused by their use of vehicles on the road. Managing occupational road risk (MORR) is a concept developed by RoSPA in 1996. It should be a continuous process and part of the way an organisation manages its operations. It is never a one-off series of ‘fit-and-forget’ technical tweaks or interventions; it's a long-term management challenge, keeping the organisation up to the mark (reducing unnecessary travel, safe journeys, safe vehicles, safe driving), and learning and improving. Important though they may be, it is not just about specific measures like licence and vehicle checking, driver assessment, driver training or even use of in-car technology to track driver/vehicle behaviours. Assess risks MORR is primarily about having the right policies, people and processes in place to work the problem, all underpinned by the right attitudes, leadership and overall safety values/culture. By getting these things right, risks can then be assessed, appropriate measures taken, outputs and outcomes can be monitored and lessons can be learned that can be fed back to improve overall road safety performance. Although it will look different in either case, this is just as true for an SME as it is for a major corporate. Those businesses that have a strategic, quality assurance (plan, do, check, act) approach to delivering against their business goals will find this idea easier to develop than those that do not. No measurement means no management. Crucially, everyone connected with the organisation’s operations on the road has responsibilities for safety, but the lead responsibility rests with the board and senior managers. It is they, helped by their advisers, who have to set and communicate expectations, approve plans, allocate time and resources and insist that the management chain makes MORR happen, providing visible, felt leadership in the way they approach road safety themselves. There is a world of difference between those organisations where work-related road safety is delegated to the fleet manager and those where there is a real team-based approach involving fleet, health and safety, HR, occupational health, safety reps, insurers, vehicle providers and others, all led by senior management and delivered, like all other health and safety outcomes, via line managers. MORR cannot just be delegated to ‘health and safety’ or to ‘fleet’ or to ‘HR’. Line managers and supervisors of all those staff who use the road in the course of their job have a key role to play. Training should not be limited to drivers – their line managers and supervisors also need training and peer support. And workers too need be involved, both as individuals and, where they have them, through their representatives. Those that ‘get’ managing for health and safety (for example, if they have achieved ISO 45001) will easily ‘get’ MORR. But those who see health and safety as just a long list of compliance actions may think MORR is just about things like licence checks, having a driver handbook, disciplinary procedures and re-training for drivers who crash, driver training for all (regardless of competence/exposure), having an accident form, banning handheld mobiles, fitting in-car technology, having higher specification cars, or circulating messages about safer driving. These interventions may or may not be appropriate, but there is often the tendency to pluck them at random out of a catalogue, when they should be carefully selected, and based on some kind of analysis and management decision-making process. But before any business can take steps to improve road safety in its operations, it needs to carry out an initial status, ‘where are you now?’, review: How many vehicles? How many drivers? How many miles? How many crashes/near-misses? Causes? Costs? Has it got a clear MORR policy, and a plan with targets? What are the objectives? Have these been consulted on? Have they been communicated? Are they ‘owned’, particularly by line managers and drivers? Have they triaged their main risks? What have they done so far to eliminate or reduce risk? What risk reduction measures have they taken? Have they trained their managers? Are they tracking their implementation? Are they checking to see if these measures are actually making a difference? Are they collecting data on and learning from accidents and incidents? Are they making time and space and involving the right people to review performance regularly against plans and targets? Are they improving? Are they rewarding and celebrating success? The aim with any initial status review should be to see what is already in place around the ‘plan, do, check, act’ cycle and to find out what is missing. There has to be a focus on the organisation's capacity to manage occupational road risk effectively, not just on the ability and motivation of their drivers to drive safely. A good test of whether there really is a joined up management approach, or whether the MORR agenda has simply been delegated to ‘fleet’, is to look to see whether drivers' line managers are fully involved (being trained and accountable) and whether there is meaningful employee engagement and consultation. Once this thorough, initial assessment and gap analysis has taken place, the continuous plan, do, check, act cycle can begin. Intelligent approach An intelligent approach will incorporate periodic and well-structured senior management performance reviews, bringing in all the disciplines to look in-depth at trends, not just crashes but upstream issues such as driver behaviours (from telematics) and attitudes (from climate surveys). And they will also look radically at other options such as optimising travel plans, reducing road travel, and integrating MORR with other health and safety issues like site transport safety, manual handling, and loading and unloading. So, organisations need to be honest with themselves – are they taking an ad hoc, ill-conceived approach to managing their road risk, or are they really being strategic in their approach? RoSPA has a range of free guidance for those unsure of the answer or encountering the subject for the first time, and for those looking to take management of their occupational road risk to the next level, we also have a range of consultancy and training services to suit. And don’t forget, the best of the best should also be entering the RoSPA Health and Safety Awards to secure recognition for their achievements and to show others what good looks like. Adam Grinsell is acting head of engagement at ROSPA. For more information, visit www.rospa.com |
|
|
|
Put your organisation in the spotlight! | 29/11/2018 |
FROM THE internationally renowned RoSPA Achievement and Sector Awards to the brand new Inspiration Awards, winning a RoSPA Health & Safety Award will raise your organisation's profile to customers, peers and stakeholders. What’s more, winners are encouraged to become part of the exclusive Awards Excellence Forum, a network of likeminded award winners offering support and sharing advice that can provide help with not only your award entry – but also safety management systems and career development. Take a look at our Award Winner case studiesto find out why almost 2000 organisations value a RoSPA Award above all others. With hundreds of organisations from across the globe having already registered for the chance to be awarded a prestigious accolade, could 2019 mark your #RoSPAWinnermoment? “Each year I am amazed by the quality of the RoSPA Award Winners and the hundreds of organisations who demonstrate their commitment to raising health and safety standards.”- Dee Arp, Director of Technical Standards, NEBOSH |
|
|
|
2019 RoSPA Health & Safety Awards | 04/10/2018 |
The RoSPA Health & Safety Awards are back with NEW awards categories and NEW sponsors, the constantly evolving scheme is the best way to recognise and reward ongoing commitment to raising health and safety standards. Alongside the much sought after and globally recognised RoSPA Achievement Awards and Competitive Trophies, we are delighted to announce the launch of new Award categories: The Inspiration Awards, which celebrate individuals, teams and initiatives that are a source of inspiration and pride worthy of shouting about, The Leisure Safety Awards, and The Safe@Work Safe@Home Award. Being an award winner unlocks countless benefits, including invitations to our Awards Excellence Forum, gain valuable CPD points and recognition from press, stakeholders, customers and much more. Register online at www.rospa.com/awards, before October 31 and save up to £65. Make 2019 a year to remember, and become part of our award winning community. |
|
|
|
RoSPA focus on machinery safety | 16/09/2018 |
EVEN WHEN workplaces are made as safe as possible, risks can still remain, which is why Machinery safety is enshrined in UK health and safety law. Those who own or manage engineering and manufacturing firms are therefore responsible for ensuring machine and equipment safety, including operatives, as well as managers. RoSPA has a suite of Machinery Safety training courses designed to guard against injury, and meet legal duties: RoSPA’s Power Press Safety course is designed to provide delegates with the knowledge and understanding to properly inspect, test and maintain power press machines to keep operators safe from serious injury. Our Abrasive Wheels Safety course will allow you to adhere to the PUWER 98 act whilst also giving your employees who use, mount and manage abrasive wheels the ability to work safely. Additionally, it offers an Abrasive Wheels Instructors course which teaches how to instruct colleagues in the safe use of abrasive wheels, set training objectives and decide what training aids to use. Not only that, RoSPA can fit around the demands of your business by offering these courses In-Company, as a flexible and adaptable alternative for delivering training to you when and where you require it. T: +44 (0) 121 248 2233 |
|
|
|
Level 3 manual handling trainers | 09/08/2018 |
MANUAL HANDLING is one of the most common causes of injury at work and causes over a third of all workplace injuries. But these injuries can be prevented by making sure your organisation is equipped with the right knowledge and skills. RoSPA’s accredited Level 3 Award - Manual Handling Trainers Course has been designed with the aim of developing a confident, motivated and professionally qualified manual handling trainer. The course will equip the trainer with the knowledge and skills to deliver bespoke and effective manual handling techniques relevant to others within their organisation, creating a healthier workforce, reduce instances of MSDs, and help meet legislative requirements and current best practice. The course adopts a blended learning approach which combines face-to-face instruction with self-directed e-learning to deliver improved costs and educational benefits that’s ideal for managers, supervisors, instructors, training officers and safety professionals who have a responsibility for training others. If you want to learn more about our Manual Handling Trainers course you can visit our website where you’ll find a wealth of information including our 10 Tips for Manual Handling infographic - which is available free to download - to help you get off to the right start. T: +44 (0) 121 248 2233 |
|
|
|
RoSPA welcomes new product safety office | 23/01/2018 |
RoSPA has reacted positively to the Government's announcement of the Office for Product Safety and Standards. The Royal Society for the Prevention of Accidents (RoSPA) has welcomed the Government’s announcement of the Office for Product Safety and Standards, in response to calls for an improved approach to product safety in the UK. The new body has been set up to provide a central technical and scientific resource to support local authorities and businesses, and was created in response to a report from the Working Group on Product Recalls and Safety, of which RoSPA is a part. Errol Taylor, RoSPA chief executive and member of the Working Group, said: “RoSPA advocates an evidence-based, cross-industry approach in its accident prevention work, and we are pleased to see the creation of a body that engenders this ethos. “In support of this, data collection on product safety issues and subsequent injuries must be improved, and we are delighted to see that the Government has recognised this as part of its recommendations, stating that 'systematic and sustainable ways to capture and share data and intelligence should be established and agreed by relevant parties'. “We hope that the new body, and the Government’s other recommendations, will lead to better co-ordination and central support and leadership for major product safety issues.” RoSPA has worked extensively on the issue of product safety and recalls, and has been part of the group which produced PAS 7100 – the code of practice for recalls. The charity has also been working with the Royal College of Emergency Medicine (RCEM) to improve data collection on injuries, recently helping the NHS to adopt the Emergency Care Data Set, which it is hoped will provide a better understanding of the causes of injuries to people attending A&E departments. |
|
|
|
Entries for the RoSPA Health and Safety Awards 2018 are now open! | 31/10/2017 |
There is no better way to show continued commitment to maintaining and improving safety standards. What’s more, completing a RoSPA Awards submission involves reflecting on and reviewing your previous year’s occupational health and safety performance. This means entering your submission is an ideal reflective activity which may count towards your continuous professional development portfolio. This year, the fabulous Ed Byrne will be on hand to entertain at the London and Birmingham Awards Gala Dinners and Andy Cameron (MBE) will be joining us in Glasgow. Before you go, watch our brand new celebration video showcasing the best of the 2017 Awards. |
|
|
|
Errol Taylor appointed as new chief executive of RoSPA | 10/07/2017 |
The Royal Society for the Prevention of Accidents’ Board of Trustees has announced the appointment of Errol Taylor as the charity’s new chief executive. Errol, who has been leading the organisation in an interim capacity since November 2016, joined RoSPA in 2004, initially heading up RoSPA’s commercial activities before developing the case for accident prevention as a public health priority and establishing RoSPA’s Ofqual-recognised qualifications business. He has been RoSPA’s deputy chief executive since 2006. RoSPA is currently marking its centenary and highlights so far have included the launch of a RoSPA exhibition at the iconic Library of Birmingham, a visit by HRH The Duke of York and the RoSPA Centenary Royal Garden Party at Buckingham Palace. RoSPA is also leading the development of a National Accident Prevention Strategy. Errol Taylor said: “I am honoured to become chief executive of RoSPA, particularly at what is such an important time for our charity. We have always been clear that our centenary should not just be an opportunity to look back and highlight past successes, but that it should also be focused firmly on the challenges that remain in accident prevention. Accidents disproportionately affect the most vulnerable members of our society – those who are young, old or disadvantaged – and this is something that we are working tirelessly to address. I am proud to lead a fantastic team of dedicated colleagues and look forward to continuing to develop RoSPA’s valued relationships with other individuals and organisations across the health and safety community.” Mike Parker, chairman of RoSPA’s Board of Trustees, said: “The Board believes that Errol’s passion for accident prevention, energy, skills and experience will ensure RoSPA’s continued success for the foreseeable future. His enthusiasm for working in partnership with RoSPA’s many like-minded stakeholder organisations should, in time, lead to a significant reduction in the burden of accidental injury.” Prior to RoSPA, Errol enjoyed senior customer-facing roles within the services, engineering and retail sectors. A Fellow of both the Institute of Directors (IoD) and the Royal Society for Public Health (RSPH), he is qualified as a Chartered Director with an MBA, an engineering degree and he is a gold grade RoSPA advanced driver. Married with three grown-up children, Errol is an advanced scuba diver who also enjoys cycling. Errol succeeds Tom Mullarkey MBE, who decided to stand down after nearly 11 years as chief executive. During this period, Tom successfully led the RoSPA team through some difficult financial and business challenges and more recently, in efforts to have the value of accident prevention recognised fully by political and healthcare influencers. Errol said: “We are grateful for Tom’s valuable contribution and the firm foundation that it provides for us to look ahead with renewed vigour, boldly stating that accidents do not have to happen.” |
|
|
|
Preventability key in healthcare rationalisation says RoSPA | 14/11/2016 |
Preventability must be at the heart of efforts to ease the rising pressure on healthcare services, says Tom Mullarkey, chief executive of RoSPA, in the charity’s latest Annual Review. In the newly published RoSPA Annual Review 2015/16, Tom asserts: “If your business is prevention, you can hardly avoid the metric of intervention that is preventability.” For children, for example, he sets out that 65% of preventable deaths, 75% of preventable hospital admissions and more than 90% of preventable A&E attendances are caused by accidents. And across the population as a whole, accidents cause 65% of preventable A&E attendances – about 7.5million. Given the rising demands on healthcare services, he describes prioritisation as 'the only way ahead', and outlines RoSPA’s analytical tool, The Matrix, which enables local authority decision-makers to make an assessment of preventability across the full range of public health issues. “The Matrix has now been tried by several local authorities leading to two incredible conclusions,” he says. “The first is that we are not, as a nation, spending our money optimally, to give our people the longest, healthiest lives. The second is that when we do the impact calculations more rationally, accident prevention becomes a major priority.” RoSPA’s Annual Review 2015/16 describes the charity’s work towards its mission to save lives and reduce injuries. Among the highlights were 3.6m views of RoSPA’s main website which contains extensive advice and information on home, road, workplace, leisure and education safety, plus an additional 2.2m views of RoSPA’s dedicated child car seats website. Across England, the total number of families to benefit from a cleaning products safety campaign reached 250,000, while 15,000 Glasgow families received safety advice about liquid laundry capsules in 2015/16 alone. The RoSPA Annual Review 2015/16 is available here. |
|
|