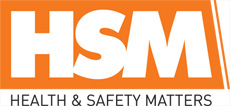
![]() |
Mark Sennett
Managing Editor |
![]() |
Kelly Rose
Editor |
Home> | Breathing Safely | >Face Masks | >Manufacturing venture of 'virus killing' PPE mask |
Manufacturing venture of 'virus killing' PPE mask
07 December 2021
VIRACOAT LIMITED'S 3 Ply Type 2R Surgical Face Mask, FFP2 Respirator Mask and FFP3 Respirator mask, a new range of antiviral and antimicrobial personal protective equipment (PPE) masks, are to be manufactured at Sudbury, Suffolk in a joint venture with The MEL Group.

Stuart Hawkins, head of group projects at The MEL Group explains, “Early last year we decided to enter the PPE mask market and designed and started production of our own in-house developed mask. Then we were introduced to ViraCoat. The ViraCoat range of masks is a very significant advance, adding a virus killing coating which makes it superior to other mask products. So, we decided to pool our resources to manufacture a world-beating product.”
The MEL Group have now developed the additional coating stage machinery and control software for the coating application and quality control, working with ViraCoat and Lancaster University, which is closely involved in testing and developing the product.
Stuart Hawkins added: “Our production line, materials and quality assurance have already met certification requirements, so we only needed to rigorously test the additional coating. Now everything is approved, we will switch our total mask production to the ViraCoat products.”The ViraCoat masks are made as a ‘sandwich’ of up to five layers of polypropylene fed in from rolls. The outer layer, which includes the ear loops, is coated on the roll as the material is fed into a custom-built tunnel oven. Specialised software controls the coating application and checks that the entire surface has been covered. The layers are then bonded, and the mask punched out.
The existing plant can produce 1.2 million masks per month and, after expansion, production capacity will reach 20million. This is anticipated to create some 90 to 100 jobs for machine operators and team leaders, who are being recruited mainly from the local workforce pool – a significant benefit to the local economy. As required, further production lines can be added in the future.
The finished masks are lightweight and soft; ergonomically shaped for comfort and to create an effective barrier against aerosol virus droplets; and have an adjustable nose bridge wire to ensure a good nose seal. The range conforms to EU Standard EN149:2001 + A1: 2009 type filtering efficiency. The company says the antiviral and antimicrobial coating begins to kill COVID-19, its variants, and other virus infections, on contact, reducing risks to staff and patients of contamination while putting on and removing the masks and when disposing of them. This means masks can be safely used for longer, which will reduce frequency of changing masks and therefore costs. New standards are being sought that will allow ViraCoat coated masks to be an even lighter, more comfortable single layer, which can be repeatedly washed or sterilised.
Jon Chadwick, CEO of ViraCoat’s parent company, ViraCorp, comments, “We are delighted to be working with The MEL Group. They have made it possible for us to bring the ViraCoat masks to market much quicker than might otherwise have been possible and their quality standards, being heavily based in the aviation and defence sectors, sit well with our vision for the product as a quality market leader.”
The MEL Group, headquartered in Sudbury, is an engineering solutions provider to aerospace, defence and industrial sectors as a tier 1 supplier to many OEM fortune 500 companies and has a presence on both coasts of the USA and across Europe. ViraCoat is a subsidiary of ViraCorp, a group of biomedical research and development companies focused on developing defence products against the viral outbreaks, pandemics, and endemics that threaten world health; the ViraCoat range of masks is the first product to go into production.
For more information, visit www.viracorp.global
- No related articles listed