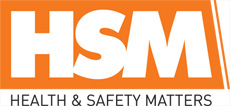
![]() |
Mark Sennett
Managing Editor |
![]() |
Kelly Rose
Editor |
Home> | PPE | >Ear Protection | >Stay in the loop |
Home> | PPE | >General PPE | >Stay in the loop |
Stay in the loop
07 November 2022
Effective communication increases productivity on high-noise sites. Sarah Baker takes a look at how to make team communication more effective while improving workplace safety and health.

PRIORITISING EFFECTIVE communication increases productivity, accuracy and efficiency, but this is not simple to achieve for all organisations. Strategies and equipment must meet the needs of users. In work environments with dangerous noise levels, unsuitable communication solutions can put workers at risk.
A report by the Project Management Institute (PMI) found that ineffective communication results in fewer successful projects. The report showed that organisations with highly effective communication report more jobs meeting the original project goals, completed on time and within budget. Organisations classed as ‘highly effective communicators’ report 80% of projects that met the original goals, 71% of projects completed on time, and 76% completed within budget; this can be compared to the results from companies classed as ‘minimally effective communicators’, who report only 52% of projects met original goals, 37% completed on time, and 48% within budget.
In construction, infrastructure and industry, communicating effectively is essential to carrying out tasks safely and efficiently however this can be difficult to achieve due to factors in the workplace and hazards present. A dispersed and moving workforce, often with multiple teams of contractors working together for short periods of time, can create a fractured working environment.
High noise levels pose an additional set of problems. Workers are unable to communicate with each other. Without the ability to talk to colleagues, ask questions, confirm instructions and warn others of danger, work becomes unenjoyable, unsafe and workers feel isolated. The requirement to limit noise to an average exposure level of 80dB for the wearer means control measures must be implemented to protect employees against hearing damage. Use of hand signals and other non-verbal communication can help with increasing safety in certain situations, but the information that can be conveyed is limited, and these methods do not help workers to feel connected to each other or improve morale. Impaired situational awareness and isolation accelerates fatigue, further impacting productivity and putting workers at risk.
Administrative controls implemented to reduce exposure can impact on an organisation’s productivity and ability to complete projects on time. One option is to limit access to the hazardous area, for example setting up the job in a different way, or to use job rotation to minimise the amount of time individuals spend on a high-noise task, with an additional option being to increase rest periods.
These controls add to downtime and can be restricted by the skills of the workforce.Technology can help organisations to communicate effectively and safely without increasing downtime. “Unified Communications” and other integrated systems are contributing to improved communication between planners and designers, architects, managers and site supervisors, but time-sensitive information can be lost if the same investment in improving communication is not extended to the vital teams on the ground.
In addition to implementing project management systems, employers must carefully assess the communication requirements of site-based personnel. Operatives must be able to communicate with each other in order to share information at the required speed in a critical situation. The provisions made for communication on high-noise sites must enable safe teamwork
Active hearing protection incorporates electronic components that interact with the external noise. Level dependent products, conforming to EN 352-4 or EN 352-7, allow the wearer to hear safe sounds – such as speech and warning signals – while attenuating high-level noise to a safe level. This enables wearers to communicate face-to-face when wearing hearing protectors. They can hear approaching hazards, remaining aware of their surroundings and in touch with the rest of the team without needing to remove PPE. The hearing protectors pick up low-level sounds, which are amplified in a loudspeaker in the ear defender cup or earplug body. When high noise is detected, the circuit is switched off, allowing the product to attenuate the sound energy to a safe level.
Electronic hearing protectors can do more to improve communication. Products with built-in intercom systems facilitate communication between operatives working at a distance from each other. Some products enable all users to communicate as a team. Other types are restricted to two-way communication, or allow safety information to be distributed to an entire workforce but do not facilitate intercommunication between operatives.
To select a suitable hearing protection communication solution, employers must identify what teams need to communicate effectively and work safely. Considerations include the size of the team or number of people to be connected, the range required to cater for the physical distance at which teams work, and the needs of the workers. If operatives need to be able to make or answer calls on the job, handsfree connectivity can offer a safe solution. High-quality audio with self-hearing features can improve situational awareness and make intercom communication feel more natural, increasing safety in hazardous areas and reducing fatigue.
The chosen products must provide hearing protection at the correct level. Noise levels should be measured; where noise is above relevant action values and exposure limits, employers should take the necessary actions to reduce exposure to a safe level. Care must be taken to ensure wearers are not overprotected. The aim when selecting suitable hearing protection is to achieve an average exposure level of 80dB for the wearer. Products with the highest attenuation are not always the most suitable. If the sound is made too quiet, wearers can be prevented from hearing warnings or other hazards, putting them at risk of an accident.
A suitable hearing protection communication solution prevents the need to remove or adjust PPE to talk to colleagues and allows wearers to work comfortably and efficiently without impediment.
Increasing productivity through improved communication must not come at the cost of safety. The challenge for many organisations is reconciling noise control with communication and teamwork. Identifying solutions that meet the needs of site-based personnel, and selecting equipment which allows wearers to talk to each other and hear their surroundings while receiving adequate hearing protection, makes team communication more effective while improving workplace safety and health.
Sarah Baker is marketing director at JSP Safety. For more information, visit www.jspsafety.com
- Sizing up the market
- David Cameron Officially Opens JSP's new Industrial Safety Helmet Manufacturing Line
- Spots a fake
- JSP's interactive DigiHUB brings PPE to life
- No more mask fatigue
- Keep the chill off
- Counterfeit safety helmet warning
- Revised PPE regulation: a significant alteration
- Fog-free vision
- Mask and specs combo simplifies fit testing