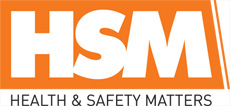
![]() |
Mark Sennett
Managing Editor |
![]() |
Kelly Rose
Editor |
Handle the heat
25 November 2021
Maria Kramer provides an insight into gloves for protection from heat and flame and helps you get up to speed with the latest standard changes.
THE EN 407 standard was revised in 2020 with several updates to support the increasing need for hand protection against thermal hazards with new test methods and product marking requirements. EN 407:2020 specifically covers PPE that protects all or part of the hand or arm against thermal risks such as flammability, contact with heat, convective and radiant heat, small splashes or large quantities of molten metal.
Products that are considered to offer protection include gloves for industrial, domestic and commercial use and thermal protective sleeves / arm protection with the exception of firefighters or welding gloves that have their own standards.
EN 407:2020 tests and what’s changed
The previous version of EN 407 defined a test method for Burning Behaviour; now titled Limited Flame Spread which is carried out according to new test method EN ISO 15025:2016. The test involves placing a glove vertically over a burner and analysing the response to ignition by a flame. Classification is based on the length of time the material continues to burn and glow after the source of ignition is removed.
Performance Level |
After Flame Time (s) |
After Glow Time (s) |
1 |
<15 |
No requirement |
2 |
<10 |
<120 |
3 |
<3 |
<25 |
4 |
<2 |
<5 |
Contact Heat is now carried out according to new test method EN ISO 12127-1:2015. The test material is placed on a calorimeter (a device that measures heat) to which a heated cylinder is then brought into contact with the test material. The time it takes to achieve an increased temperature of 10oC on the calorimeter once the heated cylinder is in contact with the sample is determined and this is called the threshold time. Classification is based on the threshold time achieved at various test temperatures.
If a level 3 contact heat is achieved, then limited flame spread must also be tested and pass level 1.
Performance Level |
Contact Temperature TC (oC) |
Threshold Time tt (s) |
1 |
100 |
>15 |
2 |
250 |
>15 |
3 |
350 |
>15 |
4 |
500 |
>15 |
Convective Heat is now carried out according to new test method EN ISO 9151:2016. The glove is placed in a controlled chamber and exposed to a flame. The resistance is based on the minimum length of time it takes to transfer the heat from the flame rather than average as per the previous version of the standard. This rating can only be used if a minimum of level 3 is achieved in the limited flame spread test, and if not, the maximum convective heat level that can be reported is a level 2.
Performance Level |
Heat Transfer Index HTI (s) |
1 |
>4 |
2 |
>7 |
3 |
>10 |
4 |
>18 |
The Radiant Heat test involves the glove being exposed to radiant heat and the classification is determined by the minimum time is takes for the transfer of heat from the radiant heat source (known as the heat transfer index RHTI24) rather than the average time as per the previous version of the standard. This rating can only be used if a minimum of level 3 is achieved in the limited flame spread test, otherwise a maximum of level 2 shall be reported.
Performance Level |
Heat Transfer t24 (s) |
1 |
>7 |
2 |
>20 |
3 |
>50 |
4 |
>95 |
Resistance to Small Splashes of Molten Metal. The glove is splashed with molten metal at a specified rate and the number of molten metal drops that are required to produce a temperature rise of 40oC are measured. The classification is based on the lowest result achieved for tested samples rather than the average as per the previous standard. Specimen are taken from the cuff, palm and the back of the glove. This rating can only be used if a minimum of level 3 is achieved in the limited flame spread test otherwise a maximum of level 2 shall be reported.
Performance Level |
Heat Transfer t24 (s) |
1 |
>10 |
2 |
>15 |
3 |
>25 |
4 |
>35 |
Resistance to Large Splashes of Molten Metal is now carried out according to new test method EN ISO 9185:2007.
The glove is lined with a PVC foil skin-simulated material and molten iron metal is poured over the glove. Once the test is complete, the liner material is assessed for any changes such as pin holing or degradation and the classification is based on the minimum weight of molten metal required to cause the changes to the skin simulated material as opposed the average weight of all samples tested as per the previous version of the standard.
If a drop of the molten metal is stuck to the glove or if the sample ignites, the material fails the test.
Note that the use of molten iron is mandatory for this test. Other metals may be tested as per specific requirements; however, the corresponding test results shall be given on the user information that is supplied by the manufacturer.
As part of the EN 407:2020 update, for all tests apart from limited flame spread, the appearance of the innermost layers of the glove shall be reported and the material shall show no sign of melting and holing.
EN 407:2020 Changes to markings
Hand and arm protection that has been tested for at least one of the tests in EN 407:2020 and achieved a minimum of level 1 may be marked with the relevant pictograms as included in clause 7 of the standard.
While the 2004 version of EN 407 used the pictogram depicting a ‘flame’ when claiming against thermal protection, this may now only be used if the product has been tested to and achieved a minimum level 1 for limited flame spread.
Figure 1 – EN 407:2020 pictogram for products tested to and achieving minimum level 1 for limited flame spread
Where the product does not claim a limited flame spread performance level, the following pictogram shall be used
Figure 2 – EN 407:2020 pictogram for products not tested to limited flame spread
The pictogram must include the scores achieved for each test underneath the relevant symbol in the following order:
-
Limited flame spread (levels 1-4)
-
Contact heat (levels 1-4)
-
Convective heat (levels 1-4)
-
Radiant heat (levels 1-4)
-
Small splashes of molten (levels 1-4)
-
Large quantities of molten (levels 1-4)
The marking of the 2 pictograms together on the product is forbidden.
Changes to other standards in glove testing
EN 388:2016+A1:2018 – Changes to the Abrasion test
The test method for abrasion resistance has largely remained the same, however there has been a change in the abradant that shall be used as brought into the 2016 version of the standard.
There was a necessity to consider changing the abradant due to various reports of inconsistent results achieved between batches. Standard working groups carried out a number of studies and have confirmed and recommended the use of a standardised grit 180 sandpaper which is cited within the updated EN388 standard.
TESTING IMAGE HERE PLEASE
This is of a finer quality and has been found to give more consistent test results. The standard now also includes a method to validate the abradant.
EN ISO 21420:2020 replaces EN 420:2003+A1:2009
The EN 420 standard was developed to give guidance on glove design and construction, resistance of glove materials to water penetration, innocuousness, comfort and efficiency, marking and information supplied by the manufacturer applicable to all protective gloves. There are a number of changes that accompany EN ISO 21420 replacing EN 420.
When it comes to glove design and construction, EN ISO 21420:2020 includes additional instruction that multi-layered gloves shall be able to be doffed without separation of the layers of the fingers
The new standard states that the protective gloves shall not adversely affect the health or hygiene of the user. The materials should not, in the foreseeable conditions of normal use, release substances generally known to be toxic, carcinogenic, mutagenic, allergenic, toxic to reproduction, corrosive, sensitizing or irritating. There is now a list of substances that shall be checked allowing manufacturers to align more with the REACH legislation on hazardous substances and substances of very high concern:
-
Where a glove is made of several materials or layers, each material shall now be tested separately for pH tests, azo colourants (dyed products) and chromium VI (leather products).
-
DMF levels shall be checked in products containing PU (polyurethane) rubber
-
Plastics and rubbers are to be tested for PAH (polycyclic aromatic hydrocarbons) levels if they are in contact with the skin
-
Metallic parts of the glove that are in prolonged contact with the skin shall be tested for nickel content
There is no longer a requirement for specific minimum glove length. Where the glove is required for a specific use, ie welders or firefighters, then the minimum glove length shall be specified within the manufacturers user information.
There is an additional requirement for gloves that are intended to be worn in areas where flammable or explosive risks exist or might be present, the electrostatic properties shall be tested according to the test method described in EN 16350. For gloves meeting this requirement, the following pictogram can be used for marking.
Figure 3 – Pictogram for EN 16350 Electrostatic Properties
The previous standard included requirements only for surface electrostatic properties or charge decay according to standards EN 1149-1 or EN 1149-3 where relevant.
Lastly, EN 21420:2020 differs from EN 420:2003+A1:2009 when it comes to marking of the products. Manufacturers must now include traceability details on the glove; these are batch numbers or the date of manufacture.
The user information accompanying the product now requires the following additional details:
-
Information on product storage conditions and whether the product may be affected by ageing. A reasonable date of obsolescence shall be given if relevant.
-
Testing for extractable proteins is no longer mandatory within this standard, however, if the product contains any natural latex, there shall be an appropriate warning stating so in the case of causing an allergic reaction to end users
-
Instructions on relevant donning and doffing of the gloves to ensure comfort and protection from contamination of the hand
-
Laundering instructions shall be available if relevant with appropriate care symbols; and where laundering is not recommended, a statement indicating the gloves are not washable
Understanding and keeping abreast of changes to EN standards can be difficult for Health & Safety Managers, Purchasing and glove users to navigate, but it’s vital risk assessments for hand protection are carried out reflecting up to date performance levels and criteria. Failure to do so particularly in work environments involving exposure to heat or flame can out workers at risk of serious injury.
Maria Kramer is technical manager at Tilsatec. For more information, visit www.tilsatec.com