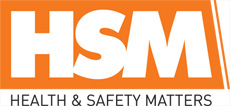
![]() |
Mark Sennett
Managing Editor |
![]() |
Kelly Rose
Editor |
Home> | Slips, Trips & Falls | >Fall Prevention | >Drop the risk |
Home> | Slips, Trips & Falls | >Fall Protection | >Drop the risk |
Home> | Premises | >Risk Management | >Drop the risk |
Drop the risk
19 June 2023
The construction sector is among the most dangerous industries in Britain and working at height is the leading contributor to on-site fatalities. Peter Upcott says that by following best practices around work safety and managing dropped objects, the risks can be mitigated.
ACCORDING TO the latest data from the Health and Safety Executive (HSE) for 2021-22, the construction sector had the highest number of fatal injuries to employees and the self-employed in Great Britain, followed by the agriculture and manufacturing sectors.
The leading cause of fatalities in industry was once again falls from height, with deaths caused by flying and falling objects also prominent on the list.
It is a timely reminder about the dangers prevalent to working at height, as well as the importance of following best practices to reduce the risk of injuries and fatalities.
Hazards in the construction industry are numerous but here we will focus on the dangers of dropped objects – i.e., any item with the potential to cause injury or death when it falls.
As industry professionals, you will be aware that the Work at Height Regulations 2005 (section 10) states that employers are responsible for taking steps to prevent the fall of any material or object – or, where that’s not practically possible, to take sufficient steps to prevent any person being struck.
To help fulfil this responsibility, risk assessors often use a dropped object calculator to identify the highest and lowest risks on a site, relative to their height and weight.
The results of this chart range from first aid cases to fatalities and are a guide only, giving a general idea of the potential severity of a dropped object - assuming that correct PPE is worn, and no sharp objects are involved.
Even if your company is meticulous with its risk assessments, however, there are likely to be times when multiple companies are working on the same site.
At these times, it is critical that the companies work together to align and allocate responsibilities and best practice.
Ten factors that contribute to dropped object incidents
Statistics show that around 30% of all dropped object incidents are related to design, technical or mechanical issues but almost 50% can be attributed to human factors.
An understanding of the primary causes of the incidents can help conduct more thorough risk assessments by considering these during work site hazard identification:
Inadequate risk assessment: A risk assessment can identify potential energy sources, index tools and equipment required for each task and increase worker awareness about the potential dangers of falling objects.
Human factors: Inadequate training or awareness of hazards, operator error, complacency, neglect and poor reporting can result in compromised safety.
Inadequately stored or secured tools: Hand tools, power tools, mobile phones and even Personal Protective Equipment (PPE) should be securely tethered with tool lanyards.
Inadequate procedures: If the management of change process isn’t in place to identify and control risk from the changes occurring in the workplace, unidentified and new risks may be missed.
Failed fixtures and fittings: Corrosion, vibration, poor design, selection or improper installation can all cause fixtures and fittings to fail and fall. Regular inspection helps monitor deterioration.
Poor housekeeping: Workplaces and tool kits should be kept organised and tidy to prevent pre-existing hazards from previous tasks.
Collisions and snagging: Moving equipment, lifting and tag lines can all cause snagging or collision. The impact of collisions can create other dropped objects and debris.
Inadequate inspection and maintenance: Regular inspections and maintenance repair schedules can help identify corrosion, damages, wear and tear to equipment and structural elements.
Redundant, neglected and home-made tools and equipment: Home-made tools, improvised tool tethers, equipment that is not certified or even damaged tools that have been subjected to a previous fall can fail or break unexpectedly.
Environmental factors: The effects of extreme conditions are more pronounced in exposed areas and can compromise the stability of equipment, tools and structural features.
How to reduce accidents on site
It is essential to communicate the expectation that dropped objects will be eliminated - and ensure that a plan and procedures are implemented.
Employers then have a duty of care to ensure their employees have the appropriate training, equipment and materials to implement the procedure effectively.
It is also the responsibility of the employer to carry out risk assessments within a workplace, although an appropriate individual can be appointed to carry this out on behalf of the organisation.
Employees must share some of the responsibility too. Through dropped object training awareness, employees should know to inform line management of any drop hazards within their scope of work and only carry out work when all hazards have been eliminated.
As always, using the correct equipment in the correct manner helps to lessen the risk on site.
Correct use of tethers and lanyards
Despite their essential purpose, there are currently no UK standards for tool tethers, anchors and containers - although this is a conversation that is gaining momentum and could change.
There are products available in the UK, however, which are typically based on the USA ANSI standard, ANSI/ISEA 121-2018, and there are very firm dos and don’ts when using them.
You need to ensure tethers are certified and rated for the weight of the tool; they are fitted by a trained person; and that the integrity of the tether is verified prior to use. If any of this is out of place, then the tether shouldn’t be used - and a tool that exceeds 2.5kg should never be tethered to a person either.
Tool weight, training and integrity are key factors for lanyards too. You should also ensure that, at full extension, they won’t impact workers below and you should fix tools weighing more than 2.5kg to a secure, fixed and rated anchor point.
It is also important to use a permanently connected or transferable lanyard when a group of small tools are being used; to transfer shock loads from a person to a rated structure; and to ensure the weight of the tools attached to the body does not overload and exceed the weight limit of the harness.
Creating a risk register
If you haven’t already, it is best practice to create a risk register. This will allow your company to maintain and track risks. It should contain the relative risk of equipment at height; the identification of equipment; the location of equipment; the methods of positioning, fastening and securing; and visual guides – e.g., photographs to monitor high risk items.
Suffice to say that correct planning, training, communication and equipment, as well as general awareness of the risks and best practices when working at height on site, are all absolutely vital to reducing the number of injuries and fatalities in the construction sector in the UK and beyond.
Peter Upcott is a PPE consultant working with Guardian Fall. For more information, visit www.guardianfall.com