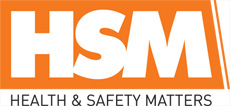
![]() |
Mark Sennett
Managing Editor |
![]() |
Kelly Rose
Editor |
Fabric of success
13 July 2021
As workers demand more from their workwear than ever before, Danny Hemmings takes a look at the key drivers in the market today.
UNDOUBTEDLY THERE has been (and always will be) a demand for workwear that offers functionality, performance and innovation together with the very best levels of protection for different hazards – such as molten metal or electric arc. However, the market is now also focusing on key areas such as inclusivity and environmental impact.
Environmental impact
As we all know, human activities are disrupting the balance of nature and the climate system. To counter climate change, everyone must help make the transition towards a more sustainable future. One of the ways users can do this with their work clothing is to make sustainability a clear priority when choosing their workwear supplier – ensuring they work with (and use products made by) manufacturers who can demonstrate a clear and robust policy towards environmental and CSR issues.
It is vital that manufacturers take an even firmer strategic grip on the issue of sustainability by using the latest environmental research and innovation to develop their protective clothing.
The latest research report from Research Institutes of Sweden (RISE) shows that the most effective way to reduce the environmental impact of clothing is to increase the useful life of garments. If we can increase the useful life of a garment by a factor of three, its carbon footprint and water consumption are reduced by 65–66 percent. This also means less waste and less demand on resources.
The challenge is to find the right balance. Sustainable product development means early assessment of various aspects that must be carefully considered. For example, some materials can have low environmental performance in the production phase, but alternatively increase the life cycle of the end product and vice versa, as materials with better environmental performance can lead to a shortened product life cycle. Therefore, it is important to make the right decision based on analysis of intended areas of use, hazard and recycling possibilities of the end product.
Research and innovation in textiles are vital if we are to continue developing applications for our protective clothing. It is important to identify sustainable materials and fibres that have unique properties. Right from the design stage, manufacturers should ensure that the smallest details meet the highest standards of safety without compromising on durability. By doing this, we can increase the useful life of protective garments and create benefits for both the user and the environment. One good example of this work is developing inherent flame retardant garments that can also be used to protect against chemicals and be completely free from fluorocarbons. Fluorocarbons do not break down in nature, so as a result, these garments with a fluorocarbon treatment leave a heavy environmental footprint and are consequently a huge polluter for the environment. By removing Fluorocarbons, we make a significant positive impact on the environment without compromising on protection for the wearer.
We all need to continue driving the textile industry towards a more sustainable future by focusing on our key development areas. Extending the life of our garments and further improving quality are an absolute must. We need to also offer the ability to repair garments as a step towards sustainable consumption. We should strive to reduce energy use, transport impact and the use of natural resources at all levels. We also need to apply better production technology that use less water, less chemicals and more sustainable materials.
However, we also realise we have a lot of work ahead of us to achieve all our goals. We see strong potential today in making use of the waste from certain types of fabric and weaving it into a new fabric. We want to find new uses for worn-out garments so that we can truly create a circular economy in our market. However, recycling of used garments is a big mountain to climb – components such as zippers, buttons, high visibility tape must be stripped out of the garment. We need to take into account where the garment has been used during its lifetime? What contaminants may be within the fibres of a used garment? But, it is imperative that we find a solution to ensuring the recycling circle can be made complete.
Inclusivity in the workplace
Today’s ever-changing workplace shows that more women are working in former male-dominated environments. In addition, many large companies are striving harder for a more equal workplace – actively encouraging woman to enter roles previously seen as male dominated. Acknowledging these changes is vital for manufacturers in order for them to take a step forward in the development of protective clothing for women.
It is no longer acceptable to cover ladies workwear just by using smaller men’s sizes. It is crucial to have the right workwear and that it fits properly, to ensure the wearer is safe. Often comfort and ergonomic issues are reasons cited for inappropriate wearing of protective clothing such as not wearing garments correctly or at all. We are all different and manufacturers must offer core ranges in a ladies fit off the shelf. Users should always look for a manufacturer that shows ongoing commitment and investment into workwear ranges for both sexes.
Electric Arc Risk
Listening to some in the market, Electric Arc would appear to be a hazard that appeared very recently - which of course could not be further from the truth.
Electric arc flashes have always been a major hazard. However, the likelihood of arc flash has fallen substantially over the years as installers started insulating switchgear, but then tool hazards became more of an issue.
With uninsulated tools, there is a high risk of triggering an electric arc. Insulated tools began to be introduced in the 1990s and came into widespread use from 1995. Despite this, there are still electric arc incidents.
There is no doubt that hazards remain today, as there is still old and unprotected switchgear in use as well as people working with overhead power lines, underground cables and uninsulated batteries. There is also a hazard of electric arcing when electrical maintenance is carried out or when doors and guards are removed and tools are used nearby.
The positive news is that never has there been such a wide variety of clothing offering arc protection - whether base, mid or outer layer garments. Combined with arc flash PPE such as helmets, visors and gloves, users are able to be better protected against the risk of electric arc than ever before.
However, poor knowledge within the supply chain means that poor decisions are being made to try and mitigate this hazard – if at all. Injuries from electric arc may thankfully be rare but when they do occur, they can be extremely serious and the user can receive life-changing or life-threatening injuries, especially to the face and hands. That is why a holistic approach should also be taken to arc flash protection, body, face and hand protection needs to be worn in unison. Better training is often required in this area so that users can understand the risks and consequences, change their behaviour and working practices by applying the correct arc flash clothing & PPE helping to minimise the risks of serious injuries.
Tranemo Workwear aims to make workplaces safer - where the correct work clothing could have prevented an accident or helped to reduce the consequences of it. For this reason, we develop new types of advanced workwear with improved flame and heat protection together with comfort and innovation. The journey we started has changed both our mission and our vision. We are now focused entirely on advanced workwear solutions and strive to become the leader in the market for inherent flame retardant workwear.
Annually, the Tranemo Group distributes over 600,000 high quality workwear garments to customers throughout Europe and the World.
Danny Hemmings is sales director at Tranemo Workwear. For more information, visit www.tranemoworkwear.co.uk