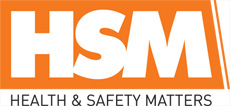
![]() |
Mark Sennett
Managing Editor |
![]() |
Kelly Rose
Editor |
Home> | Handling & Storing | >General Handling | >Addressing manual handling's blind spot |
Home> | Handling & Storing | >Safer Manual Handling | >Addressing manual handling's blind spot |
Addressing manual handling's blind spot
16 July 2024
INDUSTRY MAY have overhauled practices around manual handling, but critical blind spots that could compromise workplace and worker safety remain, says Richard Cutler.

According to Unison, one third of work accidents are caused by manual handling. Additionally, 300,000 people in the UK suffer back pain due to manual handling accidents every year, with the Health and Safety Executive reporting 1.6 million working days being lost annually due to manual handling injuries.
While these are sobering numbers, these statistics alone do not tell the real story. The toll manual handling injuries take on employees can be considerable, including damage to the back, neck or spine can lead to extreme pain, temporary incapacity or permanent injury.
Industry has been responded quickly by identifying the major causes of manual handling injuries in their operations and rectifying them. Robots are now a common sight for end-of-line work, with forklifts and scissor lifts, conveyor systems and overhead cranes also used for the transfer of components and equipment around a facility.
Things are better, but a critical ‘blind spot’ remains in many industrial and manufacturing plants that continues to threaten the welfare of employees and leave employers exposed.
That blind spot would be what we call the ‘first lift’ or ‘last lift’ of a heavy component, tool or piece of equipment from a transporter, such as a forklift, onto a storage solution, such as racking, or vice versa.
For example, an injection mould, press or progression tooling, welding, drilling and boring jigs, heavy batteries and gearboxes or CNC tooling will often be heavier than the recommended maximum manual lifting weight of 25kg or 55lb. Transporting these components around a plant environment will typically require lifting, lowering, carrying, pushing and pulling by either an employee or by equipment such as a forklift.
It is common for this equipment to be housed in a cramped or forgotten storeroom full of storage racking. This overlooked part of a plant can present acute dangers for employees. During the manual handling process of moving the equipment from the storeroom racking, keeping the spine upright can be difficult, as can avoiding the twisting, bending and reaching movements that may cause musculoskeletal injuries.
Even if you wanted to automate the lifting of a mould from racking onto a scissor lift, for example, it would take years for a business to see a return on investment for this expense – well beyond normal industrial investment criteria.
Consequently, employers are in a difficult position. The Manual Handling Operations Regulations require an employer to carry out a risk assessment on all manual handling tasks that pose an injury risk and, in turn, mitigate that risk. However, possible solutions are often expensive and ill-suited for operation in confined spaces such as storerooms. Robots, for example, require a considerable safety zone working area that would dramatically reduce storage capacity.
A low-cost, easily installed solution is needed for this first-lift and last-lift problem. The answer may lie in the use of omnidirectional ball transfer units, expertly designed to facilitate the movement of tools and other equipment around a storage facility and onto a transporter. Requiring neither power nor software, they can be installed and quickly implemented in existing racking systems.
The ball transfer unit provides a roll-on, roll-off capability well-suited to confined spaces. In areas where fixed tracks or suspended cables are either impractical or pose risks without proper maintenance and where there is potential for workers to come into contact with them, such solutions hold a similar appeal.
Safety is inherent in the design with components moving slowly over the ball transfer units at worker-designated speeds depending on their comfort levels – not the speed designated by the automation system.
Additional safety features such as J-plates can be incorporated to prevent equipment or components housed on the racking from accidentally rolling off. They are a safe and, crucially, movable alternative to fixed guards and can be removed completely when racking is reconfigured or relocated.
In operation, the employee simply moves the scissor lift or other transporter to within range of the racking, lowers the J-plate and gently pushes the equipment onto the lift or back onto the racking with no lifting, twisting or bending.
Considerable loads greatly exceeding the normal manual handling capabilities of a worker can therefore be moved quickly and easily with minimal risk.
While industry has made great progress in identifying and mitigating manual handling risks, critical blind spots persist, and are often found in overlooked plant areas not subject to the same level of scrutiny as other parts of the facility. Low-cost, effective solutions do exist and it is important for employers and employees that these solutions are given an opportunity to reduce injury risk even further.
Richard Cutler is engineering manager at Alwayse Engineering. For more information, visit www.alwayse.co.uk.
- No related articles listed