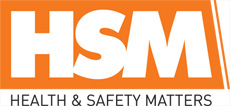
![]() |
Mark Sennett
Managing Editor |
![]() |
Kelly Rose
Editor |
Home> | Handling & Storing | >Goods Lifts | >The ins and outs of GO lifts |
ARTICLE
The ins and outs of GO lifts
29 April 2013
'Goods-only' (GO) lifts can reduce manual handling in the workplace and its associated health and safety risks - but only if they are used and maintained correctly, explains Mike Carp

'Goods-only' (GO) lifts can reduce manual handling in
the workplace and its associated health and safety risks
- but only if they are used and maintained correctly,
explains Mike Carp
If your commercial building has more than one floor, the chances are you also have a lift. This lift will fall into one of two categories: it will be either a goods-only (GO) or a goods-andpassenger lift. Each has its own health and safety requirements, which are based on the loads they are designed to carry.
As you can imagine, the requirements for a passenger-carrying lift are more stringent than for GO lifts. Passengers need to be protected so those EN81 lifts have to be regularly assessed by a 'Competent Person' (CP). Premises with a traction (rope hauled) passenger lift very often need to have at least two trained engineers to attend the site, to deal with any passenger rescues in the event of a lift becoming stuck in transit. Only one engineer is generally required if the lift is operated hydraulically.
Operators of GO lifts do not have to comply with those requirements. As a result, they are not usually fitted with 'sinking car' arrest gear, which prevents uncontrollable descents, nor any means of communicating with the outside world.
Since 1997, all passenger lifts are required to have an automatic telephone connection, to enable the summoning of a rescue service. But GO lifts do not have this facility. This means they are very dangerous for anyone who decides to use a goods-only lift to travel between levels.
We were called out to an incident recently, where people had loaded their items into a GO lift, which then became stuck. The engineer rightly instigated a descent, which is the normal practice for stuck GO lifts, thinking there were no passengers in the lift - but there were! Fortunately, because we fit safety gear to all of our lifts as standard, this did not lead to any injury to the engineer or the people in the lift - but it could have been very dangerous.
Health & safety requirements For this reason, the main health and safety requirement for GO lifts is to display clear, unambiguous warning signs - which must not be defaced - around the lift, to dissuade people from travelling in them.
This applies even if the person does not intend to travel in the lift. Most people push their goods into the lift, and so their hands are the only part of their body which enters it. Often this is done using a pallet truck or a forklift but it can be any method which means the person doesn't have to enter the lift. However, taller GO lifts at a height of more than 1800mm are highly prone to misuse as people will often enter the car for loading purposes.
The units can therefore risk lives whilst statically supporting persons when parked at the relevant landings. Failure to display warning signs could cause problems when claiming on insurance policies, in the event of an incident.
Under the Lifting Operations and Lifting Equipment Regulations 1998 (LOLER), GO lifts also have to be fully inspected by a Competent Person, although not as often as a passengercarrying lift. A Competent Person is described by the Health and Safety Executive (HSE) as someone who has sufficient technical and practical knowledge of the lift, to be able to detect any defects and assess how significant they are. If in doubt, ensure the CP has relevant BS EN ISO/IEC 17020:2004 accreditation, as this demonstrates their competence in carrying out assessments.
Thorough examinations of components, including suspension ropes and chains, braking systems and hydraulics, are required at least once a year. This is in contrast to goods and passenger lifts, which require an inspection at least every six months, and certain supplementary tests in the interim.
Organising the inspection is the responsibility of the duty holder, or whoever is responsible for the safe operation of a lift used at work. This could be the lift owner, a facilities manager or supervisor. Alongside this, the lift should be registered with insurers - we have been to a number of sites where the lift has never been listed, which suggests the lift is unlikely to be regularly inspected or properly maintained.
The key consideration at all times is the safety of people using the lift to transport their goods. The duty holder has a basic responsibility to ensure people don't try and use the lift for their own transport.
Failure to do so could lead to a major incident which endangers the passengers and those attempting to rescue them.
Mike Carp is sales director at DeSeM Lifts
If your commercial building has more than one floor, the chances are you also have a lift. This lift will fall into one of two categories: it will be either a goods-only (GO) or a goods-andpassenger lift. Each has its own health and safety requirements, which are based on the loads they are designed to carry.
As you can imagine, the requirements for a passenger-carrying lift are more stringent than for GO lifts. Passengers need to be protected so those EN81 lifts have to be regularly assessed by a 'Competent Person' (CP). Premises with a traction (rope hauled) passenger lift very often need to have at least two trained engineers to attend the site, to deal with any passenger rescues in the event of a lift becoming stuck in transit. Only one engineer is generally required if the lift is operated hydraulically.
Operators of GO lifts do not have to comply with those requirements. As a result, they are not usually fitted with 'sinking car' arrest gear, which prevents uncontrollable descents, nor any means of communicating with the outside world.
Since 1997, all passenger lifts are required to have an automatic telephone connection, to enable the summoning of a rescue service. But GO lifts do not have this facility. This means they are very dangerous for anyone who decides to use a goods-only lift to travel between levels.
We were called out to an incident recently, where people had loaded their items into a GO lift, which then became stuck. The engineer rightly instigated a descent, which is the normal practice for stuck GO lifts, thinking there were no passengers in the lift - but there were! Fortunately, because we fit safety gear to all of our lifts as standard, this did not lead to any injury to the engineer or the people in the lift - but it could have been very dangerous.
Health & safety requirements For this reason, the main health and safety requirement for GO lifts is to display clear, unambiguous warning signs - which must not be defaced - around the lift, to dissuade people from travelling in them.
This applies even if the person does not intend to travel in the lift. Most people push their goods into the lift, and so their hands are the only part of their body which enters it. Often this is done using a pallet truck or a forklift but it can be any method which means the person doesn't have to enter the lift. However, taller GO lifts at a height of more than 1800mm are highly prone to misuse as people will often enter the car for loading purposes.
The units can therefore risk lives whilst statically supporting persons when parked at the relevant landings. Failure to display warning signs could cause problems when claiming on insurance policies, in the event of an incident.
Under the Lifting Operations and Lifting Equipment Regulations 1998 (LOLER), GO lifts also have to be fully inspected by a Competent Person, although not as often as a passengercarrying lift. A Competent Person is described by the Health and Safety Executive (HSE) as someone who has sufficient technical and practical knowledge of the lift, to be able to detect any defects and assess how significant they are. If in doubt, ensure the CP has relevant BS EN ISO/IEC 17020:2004 accreditation, as this demonstrates their competence in carrying out assessments.
Thorough examinations of components, including suspension ropes and chains, braking systems and hydraulics, are required at least once a year. This is in contrast to goods and passenger lifts, which require an inspection at least every six months, and certain supplementary tests in the interim.
Organising the inspection is the responsibility of the duty holder, or whoever is responsible for the safe operation of a lift used at work. This could be the lift owner, a facilities manager or supervisor. Alongside this, the lift should be registered with insurers - we have been to a number of sites where the lift has never been listed, which suggests the lift is unlikely to be regularly inspected or properly maintained.
The key consideration at all times is the safety of people using the lift to transport their goods. The duty holder has a basic responsibility to ensure people don't try and use the lift for their own transport.
Failure to do so could lead to a major incident which endangers the passengers and those attempting to rescue them.
Mike Carp is sales director at DeSeM Lifts
MORE FROM THIS COMPANY
- No related articles listed
OTHER ARTICLES IN THIS SECTION