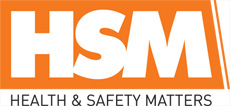
![]() |
Mark Sennett
Managing Editor |
![]() |
Kelly Rose
Editor |
Home> | Slips, Trips & Falls | >Fall Prevention | >The 360 approach |
Home> | Slips, Trips & Falls | >Fall Protection | >The 360 approach |
Home> | PPE | >General PPE | >The 360 approach |
The 360 approach
14 February 2022
When working at height, it is important to consider all potential requirements such as height safety PPE, provision for rescue, safe access, installed lifeline systems, dropped object prevention, training and inspection. Peter Upcott provides an example of height safety simplified.

WHEN AN end user has a realisation that they need more than just a training provider, but a provider of expertise, insight, and knowledge, it can become a complex process. We (safety professionals and senior managers) have all found ourselves in situations where we don’t know all the answers and seek expertise from outside of our organisations.
The challenge we have is to obtain the correct knowledge and guidance from our contacts and relying on our suppliers to connect us. This is not always as easy as it seems, especially when our suppliers don’t have a detailed knowledge of what is required, and often conflicting advice is presented which makes decisions difficult to make. In the current pandemic, expert resources are increasingly difficult to find and the market for good talent is fiercely competitive.
Height safety is a complex area and there is not always an obvious solution to safely accessing high areas. Falls from height are one of the main causes of occupational fatalities and major injuries – according to the BSIF, an average of 37 people die every year because of falling from height. The Working at Height Regulations give companies guidance on how to work safely at height and it is important that any fall protection system is designed, installed, and maintained in line with best practice and industry guidelines. Utilising an expert can be very beneficial to assist companies to understand best practice. Industry groups such as the BSIF Height Safety Group, Work at Height Safety Association (WAHSA), Lifting Equipment Engineers Association (LEEA) and its members are a great resource to assist companies with their height safety and lifting requirements. The BSIF Height Safety Group is actively supporting training and development, focused on improving skills and is currently developing a scheme to recognise different levels of competency in the industry.
This article uses a case study example to show how working with a specialist manufacturer providing multiple products and expert services can really help to find effective solutions to complex issues, as well as improving both efficiency and safety on site.
Bespoke package
The customer in this case study is a global logistics, robotics, and software provider, who had multiple requirements for working safely at height. The initial enquiry was for the provision of a working at height and rescue training course for multiple employees across multiple locations. The training provider visited one of the locations to discuss the customer’s requirements in detail and to design a bespoke training package that would meet their specific requirements. Initially this was designed for senior managers.
The training provider designed a bespoke training course, including course content, lesson plans, presentations, and course assessments. The programme kicked off with a pilot session delivered on location to the senior management team, to ensure note just a high level of attendance and engagement, but also embedding a commitment to the training programme and the importance of height safety throughout the organisation.
It is vital to get the senior team on board before then engaging the whole organisation who will be crucial in developing and adhering to safe systems of working at height. This includes training employees on the actual PPE and specific equipment they will be using, making sure a thorough understanding is embedded at every level. In this scenario, the customer ordered the correct PPE in advance of the main training programme, which enabled the customer to be trained on how to use the specific PPE, which was key to safe work in their working environments.
As a result of the site visits and discussions with employees at all levels of the organisation, it became clear that there were significant further training requirements, and the programme expanded to cover the need for systems for safe access, rescue techniques, height safety PPE advice, rescue equipment solutions, PPE and equipment inspection, installation of fixed lifelines and dropped tools prevention. The training provider was part of a large organisation with the right experts who were able to provide all the above products and services and to ensure compatibility and alignment to the customer’s needs.
Joined-up expertise
The training provider connected the customer to different areas of their business, bringing in expertise from PPE and dropped tools product specialists and engineered systems teams to develop specific solutions and to ensure that the products and services provided was fully aligned to the customer’s needs.
The benefit to the customer was invaluable due to the connectivity of the different solutions and the joined-up expertise the training supplier could call upon. Being able to rely on one contact to coordinate a full solution for a complex safety area, significantly improved safety on site efficiently and helped reduce costs for the customer.
So how did this story develop? Once the training courses were established, additional requests for systems and processes naturally developed. For instance, dropping radios and tools from height, causing potential safety issues to those below and the knock-on significant business costs, was a risk that the customer found difficult to control. Whilst there isn’t a current dropped objects prevention standard in the UK (or Europe), there is an adopted standard in the USA. Dropped objects can cause injuries and even fatalities in addition to the expense of replacing broken objects and loss of time. The training provider was able to connect the customer to a dropped tools product specialist and a solution was provided, including training, which has eliminated the customer issue. In a wider context, there are discussions to develop an equivalent dropped objects standard for the UK; in the meantime, at least, there is a solution available from multiple manufacturers.
Installation of engineered systems is often treated as a separate business from a typical supplier of height safety PPE or height rescue solutions. The benefit of having an integrated solution can be beneficial to the customer. In this case, using the knowledge gained from understanding height safety requirements in a training environment maximised the opportunity of getting the system requirements right first time. The PPE acquired can also be specified correctly and any potential rescue scenarios can be planned effectively, always ensuring best safety practices. During the programme, the customer had a system of vertical and horizontal lifelines installed and training was expanded to include the new systems to keep the processes and learning relevant and up to date. Permanent lifeline systems make working at height typically much simpler and safer for the customer.
Essential requirements
Height safety PPE and rescue equipment requires regular inspection to ensure the integrity and safety of the equipment in use. This is an essential requirement since it is not always obvious how the equipment has been treated, used, or stored. An independent company will assess products based upon factual requirements, ensure any defective item is removed from service, and facilitate the supply of replacement products to maintain safe working and compatibility of equipment and process.
Having a professional training provider on site can also provide additional expertise in relation to supplementary equipment and compatibility with existing equipment. The training provider can provide expertise and support in meetings and visits to external suppliers of supplementary equipment to assist with selection of appropriate product and suitable options.
Over the last few years this customer has benefited from the 360-approach to fall protection service, being able to rely on one company to receive a full range of height safety services from training and development, equipment supply, specialist consultancy, regular inspection, drop prevention and system installations.
The customer in this case study obtained a lot of value from the training provider and their colleagues. The 360-approach proved to be successful and is a valued methodology embedded across the organisation to ensure a complete reliable and efficient solution for the customer. When working at height, it is important to consider all potential requirements, which could include height safety PPE, provision for rescue, safe access, installed lifeline systems, dropped object prevention, training and inspection. The customer not only needed all the above equipment and services but learned during the process that their requirement for height safety extended far beyond the initial requirement and into areas which wouldn’t have been uncovered had it not been for the expert advice from the training supplier. As a result, today the customer has a much safer working environment with clear procedures in place and has significantly reduced the risk of injury from height both for people and equipment falls. Working with the many experts within one provider has given the customer the reassurance that their height safety needs are in very safe hands, with the bonus of both time and cost reductions too.
A great example of height safety simplified.
Peter Upcott is the interim marketing manager for Guardian Fall and the owner of PPE Specialist Ltd. For more information visit guardianfall.com.