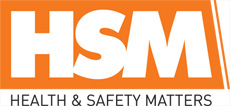
![]() |
Mark Sennett
Managing Editor |
![]() |
Kelly Rose
Editor |
Home> | Handling & Storing | >General Handling | >Blowing hot and cold |
Blowing hot and cold
21 August 2024
Meat, Fish, flowers, pharmaceuticals – they all have one thing in common. They all need cold storage to keep them fresh and viable as they travel from field and factory to market.

IN EUROPE alone, it’s an industry currently valued at nearly $140bn (2022) and projected to reach more than $575bn by 2031, with a 17 per cent per annum (CAGR) between now and 2031 (Market Research Update figures – March 2024). The growth is primarily driven by consumers’ desire to eat fresher food and to buy online.
But some chill winds of change are blowing through the cold supply chain. Strict regulations govern cold chain logistics in Europe to ensure quality and safety across three main areas: transportation; packaging; and product monitoring. Transporting and storing perishable goods comes with all kinds of challenges and the need to maintain constant temperatures to avoid contamination or spoilage.
Keeping up with regulation can be challenging. An equal challenge is the need to control costs. So, what can cold warehouses do to enhance the integrity of cold chain storage?
Dock design
First consider upgrading any loading dock to the new gold standard drive-through system. Trailers can back into the dock before breaking the seals which means goods are not exposed to outside temperatures or contaminants.
The system has two core components. The first is a vertical storing leveller, enabling the loading dock door to close directly onto the pit floor, reducing exposure to the outside air and securing the dock. It also keeps boots off the drive approach and people out of harm's way and lowers the risk of theft, tampering or injury.
A second component is a specially designed drive-through dock. Dock sealers provide a tight four-sided perimeter seal with the trailer, allowing the doors to be fully opened and closed during loading and unloading. The 360 degree seal stops warm airflow into the warehouse.
Condensation and frost problems
Warm airflow into warehouses commonly causes condensation on concrete floors and on windows. Refrigeration warehouses are required to verify and document solutions to frost and condensation build-up, with building defects no longer an acceptable excuse. Regulators wants to prevent water from dripping onto and compromising the quality and safety of stored food and pharmaceuticals. Condensation is often a factor in cases of Listeria, for instance.
There are two potential solutions to fix condensation and frost on the floor. First, any gaps between trailers and the perimeter of the loading dock must be sealed to prevent warmer outside air from entering the warehouse, hitting the cold concrete floor and forming a slippery surface of condensation.
In many warehouses, there can be a temperature difference of over 20 degree F between the cold floor and warm ceiling. High-volume, low-speed (HVLS) fans can reduce the temperature difference to one degree by mixing the air. The warmer it is at floor level, the less condensation will form, and the less likely worker or forklifts will slip and fall.
Another slip hazard is frost on the floor. It is often found near freezer doors or temperature zone separating doors. As frost piles up, doors may not close properly, causing temperature fluctuations. Blast freezer doors which can be up to 25-foot square, typically become heavily laden with frost. Employees find them so hard to open that they can resort to using a forklift truck which is hazardous to them and the freezer.
But customised curtain walls explicitly designed for blast freezers can form a safe and affordable airflow and thermal barrier to help prevent frost build-up and temperature fluctuations. They open and close quickly to restrict warm air flows into and around the freezers. Doors are available that operate at 25m/sec, helping keep food and pharmaceutical products at strict or mandated storage temperatures. As the curtains are light, they are easily used by a single person, preventing hazards to workers. The curtains are also strong enough to stop a forklift truck and prevent severe accidents with forklift trucks.
Safety solutions
Employee safety is also being improved. Loading docks are dangerous places as forklifts zip around pallets, people and products in tight spaces, and the occasional trailer creeping, tipping-over, or prematurely pulling away from the dock. Nearly a quarter of all industrial injuries occur at the loading dock.
Safety at loading docks can be improved with technologies, such as motion sensors and LED lights, to prevent people, pallets and forklifts from colliding or to ensure dock workers are hauled away inside trailers by mistake. Audio and visual alarms can warn workers in the drive approach of a vehicle backing towards them, and vehicle restraints can come equipped with LED lights indicating a trailer’s docking status. These systems, used as standard alone units or integrated safety systems, improve safety at loading docks.
As the demand for storage space rises, cold storage units grow taller. Safety systems are available to protect employees working on an elevated platform. Dual reciprocating barriers, for example, create a controlled access area with an outer gate which only opens when an inner door is closed and vice versa, so employees are protected.
A similar system can be used for multi-level pick platforms, which are often small spaces integrated into the racking system. The barrier is typically incorporated into the existing rack structure to save space. Leading models can fit in almost storage space.
With today’s “smart” touchscreen technology, workers can safely troubleshoot heavy machinery without needing personal protective equipment. They can access real-time data to operate high-speed doors to HVLS fan controls and integrate equipment into building management systems (BMS) and security systems to create a safer environment for products and people.
New technology
New digital technology is also being used to respond to regulations in respect to data, and specifically the shipping, transit and temperature control data generated across the food and pharmaceutical supply chains.
Products now have wireless radio frequency tags or RFID tracking technology. It can integrate into a warehouse management system, replacing bills of lading or packing slips and simplifying workflows by monitoring a product’s current location and its route across the warehouse before being shipped off to its final location.
Block Chain Smart Ledgers also track goods. These secure online databases house contract ledgers for goods exchanged between suppliers and receivers. Contracts can be managed, details of required storage temperature exchanged, and the shipment of goods can be monitored for spoilage, tampering and theft all along the supply chain.
Cold storage warehouses and distribution centres may also find new technologies to help lower the incidence of theft. Product thefts reported to the TAPA EMEA Intelligence Systems from supply chains in Europe, the Middle East and Africa averaged nearly €1m every 24 hours in the first six months of 2023. It is not a small problem.
For the cold storage industry, there are huge changes happening. Some new technologies, such as loading bays, or safety barriers, are not complicated upgrades but are necessary to conform to regulatory standards for cold supply chain integrity and employee safety.
Thorsten Mauritz, European marketing manager, Rite-Hite Europe
For more information, visit www.ritehite.com
- Rite-Hite advises on how to best 'close up for winter'
- Guide to loading bay safety
- Rite-Hite's HVLS Revolution fan keeping climbers cool at Boulder Central
- Acquisition
- Helps eliminate excess lifting
- Lighten the load
- Eclipse Dock Shelter's for European customers
- See the light with LED dock illumination
- Rite-Hite invests in new dock leveller production
- Keeps temperatures constant
- Reel handling solutions
- See the light with LED dock illumination
- Prevents drive-offs
- Major loading bay project
- New innovations
- Savings get the green light from Stertil Stokvis
- Light fitting looks after local sea turtle population
- ATEX loading bays
- Tailored loading bay design
- Support for surveillance