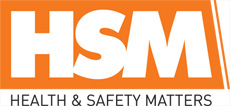
![]() |
Mark Sennett
Managing Editor |
![]() |
Kelly Rose
Editor |
1/2 (1 to 10 of 15)
Executive comment | 28/11/2023 |
---|---|
Chris Quarrie puts the spotlight on championing musculoskeletal risk reduction though the MSD awards. HSE’S LATEST ill health statistics published last month, show that there were an estimated 473,000 workers affected by work-related musculoskeletal disorders in Great Britain. HSE and CIEHF’s Risk reduction through design award aims to showcase the innovative approaches businesses are taking to reduce musculoskeletal risks. With the festive season and submission deadline rapidly approaching, the Health and Safety Executive (HSE) are inviting companies to submit nominations for the prestigious musculoskeletal disorders (MSDs) ‘Risk reduction through design awards’ 2024. Now in its 7th year, the CIEHF and HSE sponsored awards have grown from strength to strength, with nominations from a wide and diverse range of different sectors including health care, construction transport and logistics, railways and manufacturing. What are MSDs? MSDs include injuries and conditions that can affect the back, joints and limbs and can be caused or made worse by work activities. They are found across most industries and are attributed to activities such as heavy manual handling, pushing/pulling of loads, stretching/twisting, awkward and constrained postures to name a few. What’s new for 2023/24? Recognising that SMEs are a fundamental backbone to UK economy by employing over half of the countries workforce we want to recognise the hard work and dedication of UK SMEs1, particularly their approach to risk reduction and demonstrating what is possible by making simple workplace changes to reduce or eliminate MSD risk. To reflect this, there will now be two categories for the awards:
How do I submit a nomination? To request an entry form please email [email protected] We will send you a Word template to complete and return to the above email address. We can only accept nominations from employers of the workers who benefit from the design changes. We cannot accept nominations from marketing companies, consultants, or designers. A maximum of three nominations per company will be accepted. So, if you are aware of any employers in the UK that have designed a solution to reduce musculoskeletal risks, encourage them to nominate the design change for the Risk-reduction through design award! Any employer whether large or small and from any sector or industry can make a nomination. For more information and to view previous winning nominations, visit: https://www.hse.gov.uk/news/msd-awards.htm https://ergonomics.org.uk/accreditation/awards/risk-reduction-through-design-award.html Before I go, commence my Christmas shopping, and double my body weight with mince pies, I would encourage you to complete your nomination form as soon as possible as the closing date for nominations is 31st January 2024. Wishing you all a wonderful Christmas and New Year, 1 SMEs are defined by number of employees. Micro (1-9 employees), Small (10-49) and Medium (50-249 employees). Chris Quarrie works in the MSD Policy Team at HSE. For more information, visit www.hse.gov.uk |
|
|
|
Executive comment | 07/12/2022 |
Helen Balmforth looks at the importance of using the power of data to drive down incident rates and celebrating the success of proactive organisations. DISCOVERING SAFETY is a programme of work, led by the Health and Safety Executive (HSE) and funded by the Lloyd’s Register Foundation, that aims to improve workplace health and safety performance globally, by using data and novel analytical techniques to provide new insights. We have been supporting organisations to be more proactive in exploiting the wealth of data that they routinely collect, using the intelligence they gain to support health and safety decision making. This has been proven to lower incident rates. In the almost 50 years since the introduction of the Health and Safety at Work Act in the UK there have been substantial improvements in workplace health and safety, particularly in the frequency of work-related fatalities. However, many industries have seen performance improvement plateauing over recent years. The more successful your organisation has been in improving health and safety performance, the harder it becomes to maintain this level of success, and finding ways of making further significant improvements can be difficult. Organisations therefore want to understand what more they can do to make sense of the routine health and safety data sets that they collect and how they can use this data to gain valuable insights that will drive further performance improvement. Data and analytical tools such as collection software and dashboards are commonly used to report on health and safety performance. The type of information that is derived from these tools tends to be a descriptive commentary on the nature of the incidents that happened, where they happened, when and to whom. In other words, the basic facts about the incidents. They don’t address the root cause. So, it is important to go further and ask questions such as: “Why did the incident happen? When might it happen again? What do we do if it does?” Knowing why you measure, how to measure, and what to measure is a good start to using the data you collect more effectively. Also, try to move the focus to upstream measures so that you can understand what analytics have predictive value. Then you’ll be working towards a more intelligent use of leading indicators to predict risk. Recognising the effort that organisations are going to in order to use their data more effectively, we want to applaud those who have taken the time to work towards the goal of predicting risk using their routine data sets. We are proud to support the Safety and Health Excellence Awards with a new category ready for the SHE Awards in April 2023: ‘Best Use of Health and Safety Data to Lower Incident Rates.’ The awards celebrate innovation and achievements in health and safety and encompass the long-established British Safety Industry Federation (BSIF) Awards that promote the importance of innovation and underline the highest standards of excellence within occupational safety and health. We’re encouraging organisations to submit nominations for our new category on the SHE Awards website. It’s a set of simple questions that could lead to your organisation getting the recognition it deserves. Have you achieved improvements in health and safety performance as a result of data-driven intelligence? If so, submit a brief outline of the project and how far you have come on the SHE website. The award ceremony will take place on 26 April 2023 at the NEC in Birmingham; we hope to see you there! If you’d like to know more about Discovering Safety, email [email protected] Helen Balmforth is head of Discovering Safety at the Health and Safety Executive (HSE). For more information, visit www.hse.gov.uk |
|
|
|
Jennifer Webster | 06/06/2016 |
Reducing the number of accidents and near misses, or just moving off that performance plateau can be incredibly hard to achieve. Given the effort and the resources it takes to put into place a robust health and safety management system, it can sometimes be difficult to admit that more needs to be done. So what do you do? Do you ignore the fact that there is an issue, or do you make the situation appear less problematic than it actually is? Neither approach is recommended. As a tactic, the latter option can have serious repercussions. We just need to think back to the Columbia space shuttle disaster for an example of how badly things can go when factual data, particularly new data, is ignored. According to the incident report, there were at least 79 missed opportunities to re-examine whether foam striking the shuttle’s fuselage during its launch could pose a problem on re-entry. Even when the evidence suggested it might, decisions were made on previously held assumptions. As human beings, we do not like to deal with the uncertainty or ambiguity that comes with the ‘what if’ or the ‘might happen’ moments. These situations make us feel as though we not in control and make our decision- making harder. Why is sometimes easy to ignore the evidence? So how do we explain why it is sometimes easier to create certainty out of ambiguity, or why we might ignore evidence that suggests an accident might happen? In order to do this, we have to look at heuristics. Heuristics are mental short-cuts or rules of thumb that reduce some of the cognitive effort we expend each day in processing information to make decisions. In his book, ‘Thinking fast, and slow’, Daniel Kahneman (2011) describes the way we think and reason through the introduction of a dual processing system or System 1 and System 2. System 1 thinking is automatic, intuitive and effortless, a legacy of evolution. System 2 is controlled, conscious and requires effort to maintain. We constantly flit between the two because we need both Systems to function. We use System 2 processes when we have to make an important decision make, where a decision is relevant to us, or when the decision results in us becoming personally accountable. However, to maintain this level of conscious System 2 thinking requires effort to so we create mental short cuts or rules of thumb (heuristics). In other words, we subconsciously look for ways of simplifying how we process information but this can introduce bias into our thinking. It is just the way the human brain is designed and even the most seasoned professional is vulnerable to these processes. The way we think influences health and safety practices Heuristics and cognitive biases influence our decision making in numerous ways. For instance, the information we receive early on in our careers often has an undue influence on how we subsequently think about a situation. This is known as the ‘anchoring effect’. It is not usual for people to continue to do a job the way they have always done it, especially if they have done the job for a long time. This is why it is so important to set the tone about what good health and safety looks like in schools and colleges and look at refresher training for those with long tenure. Another type of bias, confirmation bias, leads people to rely on evidence that fits with pre-existing beliefs or thoughts so like the shuttle disaster, decisions are based on we know from the past without considering the unexpected. Decision-making in the corporate world The expectations of the corporate world for certainty, control and accountability also influences how decisions are made. To go to a senior manager with a ‘what if’ or a ‘might happen’ is the death knell for many a career. Instead, it is easier to blame individuals or teams who do the job on the ‘shop floor.’ The ‘fix’ is usually further training, more processes and procedures or some penalty. Consequently, nothing much changes, but what this scenario creates is a self-perpetuating cycle where the flow of information up the chain of command, the ‘what if’ or the ‘might happen’ begins to stall. Cover-ups become the norm. Worst still, the probability of a major incident occurring is played down and the focus on more short term solutions which only tackle the tip of the iceberg. Widening out the conversation This is a very brief overview of the complex world of decision-making, and there is a great deal more that is worth exploring in relation to occupational health and safety. Just raising awareness that we are all subject to heuristics and biases is a start. What we can also do is look at opportunities to increase participation in health and safety decision-making within organisations.
|
|
|
|
New HSE statistics poster | 02/11/2015 |
The Health and Safety Executive has released its annual health and safety statistics on work-related injury, ill health, enforcement and costs in Great Britain. To enable health and safety professionals to easily educate employees about the consequences of poor health and safety, HSE Books has produced an infographic-style poster which visualises the key information of the 2015 statistics.
The latest figures show that more than a million people are being made ill by their work, costing society £14.3 billion. Despite Britain remaining one of the safest places to work in Europe, injury and ill-health statistics released by HSE show that an estimated 27.3 million working days were lost due to work related ill health or injury in 2014/15. In the same year 142 workers were killed, and there were 611,000 injuries in the workplace. Of the estimated 1.2 million people who suffered from a work related illness, 516,000 were new cases. Find out more or order HSE's 'Vital Statistics 2015' poster online. |
|
|
|
Footwear of the future | 22/09/2015 |
The Health and Safety Laboratory (HSL) has announced the first of 2016’s GRIP ratings for safety footwear. According to HSE statistics, over 50% of major injuries result from slips, trips and falls. The GRIP scheme, introduced in 2014, scientifically tests and rates safety footwear for slip resistance. Companies investing in GRIP-rated footwear have reported significantly fewer slip-related accidents. Using a star rating system, where a one-star rated shoe is recommended for low-hazard workplaces and a five-star shoe suits environments that present a high risk of slipping, the GRIP scheme enables buyers to identify the most appropriate footwear for their workplace. The 2016 GRIP ratings benefit both for footwear manufacturers and buyers. For manufacturers, a GRIP-rated sole raises the profile of footwear among retailers and their customers. For buyers, GRIP-rated footwear means fewer slip accidents, and therefore lower costs, fewer staff absences and sustained productivity. Meet the team of experts on Stand E1, 7-8 October and find out more about the latest products, training, and services from the HSL. www.healthandsafetyevents.co.uk Stand E1 |
|
|
|
ORR and HSL to develop and promote use of risk management model | 06/07/2015 |
The Office of Rail and Road (ORR) and Health & Safety Laboratory (HSL) have agreed to collaborate on the development, promotion and wider use of the Risk Management Maturity Model (RM3). ORR developed RM3 as a tool for assessing and managing an organisation's ability to control health and safety risks, to help identify areas for improvement and provide a benchmark for year on year comparison. RM3 is helping guide the rail industry to excellence in health and safety risk management. Best performing companies are those which have fully integrated health and safety practices into their culture. RM3 sets out criteria for policy, governance and leadership which describe the steps used to evaluate a company’s progress from ad-hoc to excellent safety management capability. It defines what excellent management looks like, including:
RM3 has been adopted by the UK railway industry and is also being taken up by the European Railway Agency and being implemented by railways in Hong Kong and Dubai. HSL, in partnership with ORR, will now develop RM3 to support the rail industry to achieve excellence in health and safety risk management. The focus of activity for the coming year will be:
To help industry learn more about RM3, HSL are organising a number of events, with an RM3 training course being held on 16/17th July, and the IOSH RM3 Practitioner Forum on 23rd July . Both of these events will be held at HSL’s Buxton site, in the Peak District. More information on RM3 is available at: http://orr.gov.uk/__data/assets/pdf_file/0013/2623/management-maturity-model.pdf Overview of the RM3 Model: http://www.hsl.gov.uk/what-we-do/rm3-model |
|
|
|
The ABC of risk reduction | 02/04/2015 |
By changing attitudes, behaviour and culture, training can allow you to make the right changes where you are, writes Jill DeNardo, head of Training at the Health & Safety Laboratory (HSL). It may not be possible to eliminate risk in the work environment but, with relevant training and the adoption of an organisation-wide safety culture, it can be significantly mitigated. In today’s organisations dealing with complex technologies and significant potential risks there is the necessity of understanding the human dimension to operations and contribution to accidents. Appropriate training can provide the skills needed to identify and make the necessary cultural and behavioural changes which enable an organisation to effectively control risk in the workplace. Training from HSL ensures that you learn from world-class experts in your particular field. If needed, additional value can be obtained by engaging them to provide further (consultancy) support to implement a combination of tools and techniques perfectly tailored to the needs of your organisation. Safety culture Safety culture underpinned the construction of the Olympic Park for the London 2012 Games; sustaining zero fatalities, this was the safest Games in history. HSL’s ‘human factors’ experts contributed to this commendable achievement and, by applying their knowledge and expertise you can ensure the development of a positive safety culture and safer behaviours within your own organisation. "All well and good,” a senior manager might say, "but surely we’re talking about attitudes and behaviours that are complex and difficult to pin down? I understand that ‘what gets measured gets changed’ – but is it even possible to measure safety culture?” The answer is yes. HSL provides the Safety Climate Tool to do just that - along with the advice, support and training you need to address key areas of behavioural and cultural change.
Obtaining the right training and tools is essential to providing health and safety managers the skills they need to make a difference within their organisation. Demand for Behavioural Change training, part of HSL’s wider Safety Culture improvement support, is increasing significantly and has been described by a delegate of March 2015’s ‘Behaviour Change’ session as: "One of the best courses that I have attended, which has provided me (with) invaluable info for implementing in the workplace.” Ensuring staff engagement requires leadership and this is why HSL now offers ‘Mindful’ Leadership training alongside its ‘Mindfully Safe courses’. Mindfulness can be simply defined as ‘present moment awareness’. This can be awareness of internal factors such as one’s own thoughts or emotions or awareness of the external environment. Mindfulness focuses upon what is happening now, rather than in the past or future, enabling an emerging situation or information to be assessed objectively and providing stability of attention and clarity of mind. By teaching techniques to improve safety awareness in the workplace, we can help make individuals and organisations safer.
Risk management tools Wouldn’t it be great to know that you’ve implemented exactly the right approach and tools to allow you to run your organisation safely, keep your workers healthy and ensure that any inspection by the regulator easily satisfies their requirements?
That’s why HSL, the specialist research and training arm of HSE, is also working closely with regulators including the Office for Nuclear Regulation and the Office of Rail Regulation. This means you can be safe in the knowledge that you’ll receive the insight into what regulators are looking for, as well as an understanding of which solutions are most effective for your business. It’s all about having a better understanding and management of risk control, highlighting areas of greatest need and consequently driving continuous improvement. To help you achieve this, HSL offer new training for assessing and managing an organisation’s ability to control health and safety risk, and for identifying areas for improvement. This training includes:
|
|
|
|
Hearing and noise matters | 09/02/2015 |
Emma Shanks, senior scientist with the Noise & Vibration Team at the Health & Safety Laboratory examines noise at the workplace and resources for workers and employers. Noise is part of our everyday lives. At work we often take precautions when dealing with tangible hazards, such as chemicals. However, because noise is invisible - and because we are used to it and even expect it - many people don’t appreciate that noise can also be a significant hazard to both health and safety. It can take years to develop a disabling hearing loss and, because hearing loss is also part of the ageing process, many people accept that it’s inevitable. Noise exposure also occurs outside the workplace, through our leisure activities and social lives. We become complacent about noise risks and although we know it causes hearing loss, we don’t think it will happen to us. Sadly, by the time you notice there’s a problem it’s too late. You already have a disabling hearing loss. Most occupational health screening will only pick up the loss when significant damage has already occurred. On average it takes a person 10 years to address their hearing loss. In 2011, 10 million people experienced hearing loss - that’s one in six people in the UK; 3.7 million of these were working age (16 - 64 years). What we forget with hearing loss is that it isn’t just deafness that is the disability. The 'Hearing Matters' publication said: "Hearing loss has significant personal and social costs and can lead to high levels of social isolation and consequent mental ill health. It more than doubles the risk of depression in older people and children with hearing loss also have an increased risk of mental health problems. People with mild hearing loss also have nearly double the chance of developing dementia and this risk increases significantly for those with moderate and severe hearing loss. Hearing loss has a significant impact on education and employment.” The extent of NIHL It is difficult to quantify the extent to which workers are affected by Noise Induced Hearing Loss (NIHL). According to ‘Controlling Noise at Work’, the Health and Safety Executive (HSE) guidance to the Control of Noise at Work Regulations 2005, it is estimated that more than 2 million people in the UK are exposed to noise levels at work that may be harmful. The 2008/09 Labour Force Survey (LFS) showed that an estimated 17,000 individuals who worked in the previous 12 months believed their hearing problems were the most serious of their work-related illnesses. However, as NIHL is not a RIDDOR reportable occupational disease, the exact number of people who are injured or at risk is unknown. The cost of NIHLClaims are rising and in 2012 alone AXA Insurance saw a 75% increase in the number of deafness claims. David Williams, managing director, Underwriting, AXA Insurance, noted: "The issue for British industry is that, as we have seen with other areas of insurance in the UK, lots of claims inevitably lead to higher premiums in order to cover the cost of pay outs. As British business struggles through a prolonged period of recession, the last thing they need is the added expense that this will bring.” Industry / sector examplesNoise is still a problem in many industries. HSE’s autumn 2014 'Think Health' campaign highlighted the issue of noise in the construction sector where NIHL is three times higher than the industry average. This campaign showed that whilst duty-holders thought that they were managing noise well, in reality there is still a reliance on hearing protection, rather than practical control solutions, with no discussions on its adequacy or suitability.
HSE-funded research carried out by the Health and Safety Laboratory (HSL) suggests that there are still high levels of noise exposure in the UK printing industry, despite a general reduction in noise levels over the last 25 years. Data gathered from a small sample of workers across a range of printing premises showed that 50% were exposed above the 85 dB(A) upper exposure action value (defined in the Control of Noise at Work Regulations 2005) and 43% were exposed between the 80 dB(A) lower and upper exposure action values. E-learning resourceEmployers have a legal duty to protect their workers against the risks to both health and safety from exposure to noise and therefore they cannot shy away from their responsibilities. Compliance, control and management do not have to be difficult, yet the most simple noise controls in the workplace are often neglected. It is interesting to note that many of us instinctively manage noise in our personal lives: we retreat into a quiet room when we want peace and quiet; we add soft furnishings to make indoor spaces quieter; we find quiet ways of doing things about the house when we don’t want to disturb a sleeping child. So how do we ensure that good practice solutions for reducing noise at home are applied in the workplace?
HSL and 3M, with extensive knowledge and experience in the fields of hearing conservation, noise regulation, management, control, measurement, training and hearing protection, have combined their skills to produce a comprehensive but simple hearing conservation e-learning resource. This resource is designed to help users understand the issues associated with exposure to noise at work and identify what actions need to be taken to protect those at risk, in line with the Control of Noise at Work Regulations 2005. There are four modules which include exercises that will help identify practical actions for individual workplaces.
Module 1 – Hearing hazards and risks: It’s a legal requirement that everyone at risk of hearing damage from noise at work understands the risks. The starter module describes how we hear and the risks and consequences of harmful noise; the physical damage done to our ears, the symptoms and the handicap we experience. Hearing damage cannot be cured, but can be prevented if we recognise where the risks are and take action to mitigate them or protect ourselves. This module helps the user recognise the types of sound that can be harmful. It explains the relationship between noise exposure, the sound level in decibels and the duration of the sound. It also explains the measures required by law to assess for everyone at risk.
On completion of the module the user will be able to: Help others to recognise the causes and symptoms of hearing loss; say why hearing conservation matters to everyone; provide an overview of the science behind hearing and sound; gain a perspective on exposure levels.
Module 2 – Monitoring noise exposure and risk assessment: This module gives the user the simple tell-tale signs of noises that can be a risk to hearing, so they can identify who might be at risk and when and where a risk assessment is required. It includes a simple step by step process for performing a risk assessment, and explains what you need to do if they find legal exposure action and limit values are exceeded. It also raises the often forgotten issue of safety in noise and recognising the risks of missing essential warning sounds.
On completion of the module the user will be able to: Identify the tell-tale signs of noise; Explain what should be done if the exposure action values and exposure limit value are exceeded; Talk to colleagues about the effect that noise has on everyone; Undertake a risk assessment for noise exposure.
Module 3 – Noise control and hearing protection: The risk assessment provides the springboard for identifying where control is required and where it will have the greatest benefits. This module helps the user understand and use simple techniques to reduce personal noise exposure by reducing the level of the noise and the time each person spends exposed to the noise. It gives guidance on the proper use and selection of hearing protection where it is still required.
On completion of the module the user will be able to: Explain how they can affect noise around them; Identify noise controls that are effective: at the source of the noise; on its pathway to the person hearing the noise; and at the person hearing the noise; Employ simple noise controls in the workplace; Understand the use of hearing protection in the workplace.
Module 4 – Using health surveillance to influence behaviours: The final test of whether noise controls are working is health surveillance. This is an essential hearing ‘MOT’ required by law for each individual who is at risk from noise. For an employer it can identify those areas where risks remain and controls are not working. For the individual it’s a personal, confidential consultation about the health of their hearing. This module takes the user through the legal requirements, how often health surveillance is recommended and the practical aspects of what happens during health surveillance. The module shows how health surveillance can be used to check noise controls are robust and reliable and improve the health and safety culture. On completion of the module the user will be able to: Explain health surveillance to colleagues; Discuss the use of health surveillance; Recognise how health surveillance can influence behaviour and productivity; Identify who should have health surveillance and how often. The hearing conservation e-learning resource will be available from the HSL products website from early February 2015 (www.hsl.gov.uk/products). Hearing conservation and noise at work In August 2012, after a day spent on the frontline with an HSE occupational health inspector, Judith Hackitt, chair of HSE, said in her blog: "What I saw last week was the extent to which longer term health issues tend to take second place to managing immediate safety risks. Things get put on a ‘to-do’ list but somehow never get done, leaving people at risk…” It’s time for hearing conservation and noise at work to be viewed in the same light as those immediate safety risks. With an ageing population, initiatives to keep older workers in the workforce and industries where noise remains a challenge, actions, not ‘to-do’ items, must be taken. With some common sense, and a bit of imagination, most of us can achieve a quieter, safer and healthier workplace. Hearing damage is preventable. |
|
|
|
Play it safe | 20/07/2014 |
A new set of playing cards, developed by the Health and Safety Laboratory (HSL), has been designed to make it easy for teams, managers and supervisors to talk formally and informally about cultural issues and other human factors that affect safety within their organisation. Each of the Safe Deal cards contains useful information and questions to start discussions in the workplace.
Up to 80% of all accidents can be attributed in full or in part to human factors. The cards are said to make it easy to raise awareness about human factors in the workplace refreshing health and safety compliance and commitment.
For more information or to purchase the cards visit www.hsl.gov.uk/products
|
|
|
|
Preventing falls from vehicles | 18/03/2014 |
In 2010/11, over a quarter of fatal injuries reported under RIDDOR involved workplace transport and around half of reported major injuries involved falls from vehicles. The Health & Safety Laboratory explains what steps employers can take to reduce the occurrence of these types of incidents. According to the latest figures published by the Health and Safety Executive (HSE), slips, trips, and falls (STFs) are responsible for more than half of all reported major injuries and nearly a third of over-seven day injuries to workers, with a combined estimated loss of two million working days annually. Add in injuries sustained from handling and that rises to around three million working days lost.
There are several factors that contribute to the high rate of STFs, some practical – such as safe access to vehicles or footwear – and some a result of working practices. For any employer seeking to reduce the risk of injury and minimise lost time, it is important to be aware of the potential hazards and how best to manage the risks.
The ideal method of preventing a fall from height is to remove the need to work at height at all, but this is often easier said than done – and, of course, the driver of an HGV still has to access his or her cab. However, it is worth considering whether loading and securing of the load can be carried out from the ground or, if this is impractical, how the driver and/or loaders can be protected.
Ensuring safe access
Access to vehicles is a significant contributory cause of STFs, whether accessing the cab, the fifth wheel area, or the load bed itself. HSL’s research indicates that the design of the cab steps and provision of access to the fifth wheel area can be problematic, with awkward changes in step height and limited space to work putting the driver at risk of slipping and falling. Slip prevention depends on physical contact between the individual’s shoes and the floor surface, and loading and unloading of vehicles is often carried out in wet, muddy, or icy conditions that can significantly reduce the grip available. The fifth wheel area is also often contaminated with oil and grease, making it even more treacherous.
Access to the load bed can be poor; fold-out ladders often have a high first step with no handholds, and can be difficult to see from above, particularly in low light conditions. While the load bed of a vehicle usually provides good resistance to slipping, problems can occur when moving from a relatively high-friction area to an area of much lower friction, such as stepping onto a tail lift or a painted or exposed metal section of the load bed.
Specifying appropriate footwear
Safety footwear tends to be purchased to protect the wearer’s feet from impact, and slip resistance can vary considerably between manufacturers and types of shoe. The situation is further complicated by the need to work on different floor surfaces: shoes with anti-slip soles that work well on an aluminium-floored tail lift, for example, may not work well on metal profiled cab steps, which require a good interlock with shoe cleats. Contaminants such as diesel or mud can also significantly reduce the effectiveness of the footwear.
Environmental considerations
Adverse environmental conditions can make loading or unloading more hazardous, and not only because surfaces become more slippery in wet or icy conditions. Sheeting, or opening and closing the curtains of a curtain-sider, can lead to falls in high winds, as the material acts as a sail and pulls the driver/loader over. Night working, particularly in the winter months when mornings are dark, increases the risk that drivers and loaders will not see the edges of the load bed or tail lift while working on the vehicle, or tripping hazards on or around the vehicle. Hot weather can lead to heat stress, with a resultant risk of fainting or dizziness that can result in the driver/loader falling from the vehicle.
Where loads have not been secured properly for transport, there is a risk that they may become unstable or move during the journey, so that – for example – they may rest on the curtain of a curtain-sider and then topple from the vehicle as the driver pulls back the curtain. The first instinct is generally to jump back, and this can result in slip or trip injuries. If a load has shifted so much that it cannot be unloaded by fork lift truck, then often the only solution is to manually unload, and this immediately puts unloading personnel at risk in a situation they may not be prepared for and where they may not have suitable footwear and/or means of access to the load bed.
The good news is that despite these pitfalls, there are some straightforward ways to reduce the risk of injury. At the purchase stage, consider specifying anti-slip surfaces, particularly in the fifth wheel area, and steps with even step heights and depths. Handrails, handholds and colour contrast markings on edges can also help to prevent falls. Provide a safe means of access, such as steps, gantries, or platforms to vehicles and make sure the loading area is well lit and there are no obstructions that drivers and loaders could trip over when walking around the vehicle.
The right footwear is key in reducing the risk of slips, trips, and falls. This summer HSL will be launching a new Footwear Rating Scheme to help companies choose the best footwear for their needs. The use of slip-resistant footwear has been shown to be effective in reducing accidents across a wide range of businesses, from vehicle distribution to catering and even door-to-door sales. Selecting the right footwear to use can be problematic, as the slip test used for CE marking of safety shoes only provides basic quality assurance, and is not useful to identify specialist footwear that can be used to control slip risk. The new Footwear Rating Scheme will simplify the selection process, allowing buyers to select a level of slip resistance to suit their situation. Footwear will have a simple star rating provided by HSL, with more stars indicating greater slip resistance.
HSL’s Falls Prevention Team also provide training and bespoke advice to companies looking to manage the risks of slips, trips, and falls. Find out more at www.hsl.gov.uk/
|
|
|