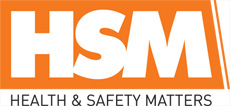
![]() |
Mark Sennett
Managing Editor |
![]() |
Kelly Rose
Editor |
1/2 (1 to 10 of 20)
Ian Richardson | 14/11/2017 |
---|---|
Making safety child’s play Cast your mind back to yesteryear, when childhood entertainment comprised a visit to the local playground, whereupon you were confronted by all manner of structures, lending themselves to imaginative adventures. The element of risk was, and still is, far removed from the consciousness of most children. Yet ask those involved in the design of such recreational facilities, and they will attest to the virtues of ‘good risk’ and the associated challenges of managing it in a way that is both constructive and important in a child’s development. So can risk be a good thing? A well designed playground offers an exciting and challenging environment in which children can develop their abilities; navigating swings, slides, roundabouts, climbing frames and other equipment can teach important problem-solving skills and help to develop physical strength, coordination and balance. Naturally, this will involve some risk-taking, and some bumps and bruises are to be expected during adventurous play. However, it is the role of manufacturers of playground equipment, and organizations that manage public play areas, to work together to prevent serious accidents and reduce the risk of permanent injury by following good practice. One suite of standards developed to assist is that of BS EN 1176 Playground equipment and surfacing. Providing EU harmonised safety benchmarks, their objective is to allow as many exciting play opportunities as possible, with as much safety as necessary. The BS EN 1176 series sets out good practice in the design, manufacture, installation and maintenance of playground equipment in public spaces, offering guidance on crucial elements such as structural strength, protection against falling, laceration and entrapment. Additional guidance to playground operators on equipment installation, inspections and maintenance, and providing clear information to consumers (site maintenance, emergency) is also covered. If the play area used by your child complies with the standards, you can rest assured that judgements, based on Europe-wide expertise, have been carried out, to balance the risk of injury with the benefits of exciting play opportunities. Furthermore, they act as a checklist to ensure that organizations don’t forget any key safety points. If an accident happens, and the equipment involved carries a label stating that it meets the standard, the insurers and courts should be satisfied that the necessary measures have been taken to set risks at the appropriate level to protect users. Standards can be used in a court of law to provide a benchmark of best practice. To find out more on the recently revised EN 1176 series, please visit: https://shop.bsigroup.com/ or contact [email protected] Ian Richardson, board director, BSIF and standards publishing manager, BSI |
|
|
|
Ian Richardson | 30/10/2017 |
How ‘smart’ should our PPE Standards be? During the recent BSIF Board meeting, which I attended, the topic of PPE and technology came up. Lots of words have been used to describe the changing face of modern protective equipment – ‘Smart’, ‘Innovative’ and ‘Intelligent’ being just a few of them. The discussion went on to mention a recent workshop organised by the CEN/CENELEC (the European Standards bodies) Sector Forum for Personal Protective Equipment, which wanted to begin looking at the potential for European Standards to cover ‘Smart garments and equipment’. Naturally, the first item on the workshop agenda was entitled: “Smart garments, textiles or equipment: what does that mean?” The conclusions from the workshop were that more consultation was necessary, and the feedback I’ve received is that in the UK the view may be that it is too early to consider a wide ranging standards development programme for Smart PPE (if that’s what we end up calling it!). However, since there has been a Standardization Request issued from the EC, in relation to ‘smart textiles’, it is almost certain that standards will be developed over the next few years. CEN/CENELEC are therefore consulting on a way forward, and would like to identify possible standardization work in the field of Smart Garments and Equipment. Some questions have been posed, for which it is clearly a priority for BSI to get feedback from the UK industry, including questions such as whether it would be useful to organize a workshop on standardization for smart PPE in the future, what is the most important product or part of product to be standardized in terms of “smart textiles”? (e.g. active high visible clothing, body monitoring systems, connections/batteries/plugs, radio transmission) and how much interest is there in participating in future standardization work in the field of PPE? (e.g. weather, chemicals, fire fighters, sports). Working with the BSIF, and other associations and organisations represented on our PPE Technical Committees, BSI will be looking to get a more in depth picture of the UK’s view on standardisation in this emerging field. If you have comments you believe will help build this picture, or would like to get involved more, please feel free to get in touch with me. Ian Richardson, board director, BSIF & standards publishing manager, BSI |
|
|
|
BSI opens gas capacity laboratory | 06/10/2017 |
BSI, the business standards company, has extended its Hemel Hempstead Centre of Excellence for respiratory protective equipment testing, with the opening of the Gas Capacity Laboratory capable of testing the effectiveness of gas and combined filters used in RPE. BSI now offers RPE testing including gas capacity testing of filters against gases such as hydrogen cyanide and sulphur dioxide which may be encountered in workplace situations in industries such as utilities, petro-chemical and agriculture, along with fire-fighting and chemical incidents. The laboratory officially opened today by Rt Hon Mike Penning MP, Member of Parliament for Hemel Hempstead. This new facility means that BSI can now offer RPE manufacturers a one-stop-shop service for masks and filters for gas and combined protection, including Air Purifying Respirators (APR) and Powered Air Purifying Respirators (PAPR) systems. This extension to BSI’s PPE services reinforces the UK’s testing capabilities, and means that BSI is both the largest PPE Notified Body and the only UKAS (United Kingdom Accreditation Service) accredited independent commercial testing and certification body in the UK capable of testing and certifying to next April’s new PPE regulations for RPE. BSI also offers testing for the internationally recognized Kitemark, as well as a range of European and ISO standards. Mark Basham, managing director, BSI EMEA comments: “From April 2018 all PPE products coming in to the market must comply with the new regulation, with just a year allowed for the transition. This is just one of a growing number of requirements globally to which manufacturers must conform, and alongside CE marking, our Kitemark™ certification offers access to a global market of the most demanding specifiers and purchasers.” The BSI Kitemark is one of the most recognised symbols of quality and safety and offers true value to consumers, businesses and procurement organizations. For consumers, the symbol means that a product has gone through rigorous testing, above and beyond the requirements of CE marking, helping to give the peace of mind that the quality, safety and reliability of their purchase is guaranteed. For organisations, ensuring their products meet the highest possible standards is a key way of ensuring they’ll continue to generate revenue into the future. The Centre of Excellence, based in Hemel Hempstead was significantly upgraded in 2014, with £5million of investment extending the range of tests and schemes it is able to support, with continuing investments planned to support further expansion of services in testing and certification. BSI currently employs more than 80 people at the site and in addition offers an apprenticeship scheme in partnership with Oaklands College, with approximately 10 students registered at present. |
|
|
|
BSI revises standard for fire detection and fire alarm systems | 13/09/2017 |
BSI, the business standards company, has revised its standard for fire detection and fire alarm systems. The standard, BS 5839-1:2017, covers the planning, design, installation, commissioning and maintenance of fire detection and fire alarm systems in and around commercial buildings. BS 5839-1:2017 Fire detection and fire alarm system for buildings. Code of practice for design, installation and commissioning and maintenance of systems in non-domestic premises is referred to in both volumes of the government’s statuary guidance for fire safety, Approved Document B, which concerns building regulations [in England] covering fire safety matters within and around buildings. The National Security Inspectorate is among organizations which consider the recommendations given in BS 5839-1 mandatory, and thus essential for contractors to follow. The revised standard is relevant to anyone involved in the commissioning, installation, design and planning of fire alarm and detection systems for non-residential dwellings. Some of the key changes over the standard it replaces include: Improved definition of the L2 fire alarm system. L2 Fire Alarm Systems are designed to offer automatic detection on all escape routes within a building The term ‘fire detection and alarm systems’, in the context of this standard, includes systems comprising of only one or two manual call points and sounders, as well as complex networked systems that incorporate a large number of automatic fire detectors, manual call points and sounders. The term also includes systems which are capable of providing signals to initiate the operation of the other fire protection systems and equipment (such as fire extinguishing systems, smoke control systems or automatic door release equipment) or safety measures (such as the shutting down of air handling systems, closing of oil or gas valves, or grounding of lifts). It does not apply to other systems and equipment themselves, or the ancillary circuits to interface with them. Recommendations for the planning, installation and servicing of facilities for operation of certain fire protection systems by the systems addressed within BS 5839-1 are given in the relevant part of the BS 7273 series. Equally, BS 5839-1 does not recommend whether or not a fire alarm system should be installed in any given premises. Recommendations for fire detection and alarm systems in dwellings are covered in BS 5839-6. Some notable organisations which the standard is expected to be relevant to include: Fire Industry Association; Electrical Contractors Association; National Inspection Council for Electrical Installation; Fire Safety Association; Loss Prevention Certification Board; National Security Inspectorate; Chief Fire Officers Association; Security Systems and Alarms Inspection Board; Chartered Institution of Building Services Engineers; British Cables Association; BRE Building Research Establishment; Institution of Electrical Engineers; National Association of Fire Officers; London Fire and Emergency Planning Authority. |
|
|
|
Ian Richardson | 24/07/2017 |
BSI began developing a new British standard for ‘Personal fall protection equipment – Anchor systems' back in March 2015. The standard will provide requirements and test methods for type testing anchor systems that are installed and tested in the base materials specified by the manufacturer for restraint systems, fall arrest systems, rope access systems, work positioning systems, rescue systems and evacuation systems. During the last drafting panel meeting some concerns were raised by BSIF representatives relating to the short time period allowed for comments on the 2nd draft of BS 8610. BSIF and BSI then entered into some dialogue about the issues which had been raised by experts on this subject, and BSI explained that the drafting group were still working on comments received earlier in the process. As a result of this collaboration, BSI agreed to continue accepting comments from the BSIF Height Safety Group with a new deadline set for the end of August. This is another strong example of where an industry body such as BSIF raising a concern, and BSI being flexible, resulted in both parties working towards the same aim of the published standard being as good as it can be. It also means the standards development process doesn’t end up being too long, thereby avoiding the risk that the intended users would not be able to gain the benefit of having a best practise document in place for them to conform to. Ian Richardson, board director, BSIF & standards publishing manager, BSI |
|
|
|
Ian Richardson | 26/05/2017 |
Keep burnout on the radar When the phrase ‘burnout’ first came into use it was seen as something that happened to other people: super-ambitious high fliers working in industries where long hours were expected and meeting unachievable targets was a condition of employment. And people in such high-stress jobs undoubtedly do crash and burn: we’ve all seen reports of high profile suicides in the City or alcohol and drug fuelled excess leading to tragedy. But burnout should be on everybody’s radar. A recognised form of work-related stress, burnout is a state of physical, emotional and mental exhaustion. You can spot the symptoms in most workplaces: the employee who is negative and cynical, the one whose performance has dropped and who lacks confidence, the one who is tired all the time, gets headaches and is irritable or slow. Both employers and individuals need to be able to spot symptoms for what they are - and know who to talk to and what to do to help. Prevention is always better than cure, though, and root causes of burnout are not as well recognised as they might be. Too much work, too much responsibility, unachievable objectives certainly play a role, but so do less obvious factors. Poor relationships at work are hugely damaging, as is monotonous work, loss of autonomy or being under-used or under-appreciated. We are living in an era of zero-hours contracts and job insecurity, swingeing cuts, redundancies and constant change. Unless this is managed effectively we’ll have a burnout epidemic. The associated negative behaviours – cynicism, irritability, presenteeism, alcohol or drug abuse - impact others, depress productivity and can skew the whole culture of a workplace. But there is plenty we can do: encourage people to take breaks, work sensible hours and have sociable non-work-related interactions with colleagues. Create a culture of trust by treating people fairly and listening to their concerns. Think about what workers are capable of and make sure you are using their skills effectively. Appreciate the efforts people make as well as what they deliver. Above all, look out for each other and don’t just accept that stress, or burnout, is inevitable. There are guidance documents available which can help you to try and tackle the risks of stress and burnout, such as BSI’s PAS 1010:2011 (Guidance on the management of psychosocial risks in the workplace) and you can get hold of a copy here: http://shop.bsigroup.com Ian Richardson, board director, BSIF & standards publishing manager, BSI |
|
|
|
Bob Wells | 26/05/2017 |
CE marking vs the BSI Kitemark - what you need to know To keep employees safe and reduce health risks, it’s vital that health and safety managers invest in the right Personal Protective Equipment (PPE). With a growing number of cheaper imports entering the market, organisations need to be aware of what to look for when choosing PPE. What is CE marking? CE marking on a product is the manufacturer’s declaration that the product complies with the essential requirements of all the Directives that apply to it. It indicates to the appropriate bodies that the product may be legally offered for sale in their country. The requirements for CE marking differ across all the Directives and may also vary for different products even within a single Directive. Depending on the product, CE marking may be as simple as formulating a technical file, or as complex as having to submit your products to regular independent scrutiny. Third party testing, systems assessment and technical file assessments may be mandatory, but sometimes the manufacturer’s unverified claim is all that’s asked for. How does the BSI Kitemark differ? For those that want to go above and beyond, the BSI Kitemark gives a higher level of assurance that a product will do what it claims. It helps differentiate well-made PPE protection products from those of a lower standard – or indeed counterfeit goods. Buyers look for the BSI Kitemark because it’s a sign of quality, safety, trust and reliability. It is also a quality mark that is used widely. For example, in the equestrian world at competitions like Pony Club meets where they specify that BSI Kitemark approved helmets must be used by competitors taking part in their events. The BSI Kitemark is voluntary, independent third-party certification. To achieve it, a manufacturer must have a comprehensive quality management system based on ISO 9001, or a recognized factory production control system combined with initial product type-testing and regularly undergo on-going audits. The BSI Kitemark shows that BSI has verified the quality of products and processes on a continuing basis. There is additional verification that the product meets the standard, as it requires regular factory visits, typically twice a year, and an ongoing product audit. Certification to, and display of, an independent BSI Kitemark provides a much stronger statement of product quality than a CE mark, giving manufacturers the ability to differentiate their products – and providing customers with genuine assurance of product quality and fitness for purpose. There are a number of BSI Kitemark schemes available for PPE standards such as EN 166 eye protection, EN 397 industrial safety helmets, PAS 015 equestrian helmets and EN 149 filtering face masks. It’s imperative that health and safety professionals buy from a reputable supplier and partner with someone that has the knowledge and expertise to keep them up to date with any changes to standards and regulations that might impact those products that are provided to employees. Bob Wells, global head of personal safety, BSI |
|
|
|
Ian Richardson | 05/04/2017 |
Walk this way A Buddhist saying states: if you are facing in the right direction all you have to do is keep on walking. During the development of ISO 45001, the forthcoming ‘Occupational health and safety management systems’ standard, around 60 countries have been participating. It has sometimes seemed doubtful that everyone would agree exactly what the right direction was, but the participants have kept moving forward and the latest draft of this much anticipated standard is now available for everyone to read. Despite some ‘political’ differences, one thing binds this project together: everyone involved is passionate about saving lives and making workplaces safer and healthier for all of us. The fact that the first draft sent out for public consultation received majority approval but did not go forward to publication shows that the concerns of the minority are respected. Over the past 10 months some critical issues have been thoroughly explored and solutions found that the majority can support. It is unlikely that anyone will declare the new draft perfect – these things rarely are – but it is another leap forward and testament to international negotiation and consensus-building. The journey is not quite over of course… The commenting phase will open in May and across the world users are being invited to read the latest draft and give their view. Regardless of whether the ballot passes or fails, the next meeting will be held in September to discuss these comments and resolve any remaining issues. At this stage, however, we are probably talking fine detail rather than radical overhaul. Those of you who read the 2016 draft may not see quite as much change in the 2017 version as you expect. Nevertheless, BSI wants to hear from you. The full draft has been made available early in the UK to allow users as much time as possible to thoroughly examine it. The UK committee will also be holding a public meeting in Swansea this June, to give people the chance to talk directly to those who are in the thick of it and who will be taking the UK’s final comments back to ISO. So let’s keep walking together and make sure that ISO 45001 achieves its goal of helping to save lives across the world. Access the latest draft via our website: http://shop.bsigroup.com Ian Richardson, board director, BSIF & standards publishing manager, BSI |
|
|
|
ISO 45001 reaches second draft for public comment stage | 05/04/2017 |
BSI, the business standards company, has published the second draft of ISO 45001 Occupational health and safety management systems – Requirements. The yet-to-be launched international standard specifies requirements for an occupational health and safety (OH&S) management system, with guidance for its use, to enable an organisation to provide safe and healthy working conditions for the prevention of work-related injury and ill health. The latest draft is now available on the BSI shop, ahead of the formal commenting period which beings on 19 May. From this date the draft will be accessible, enabling those with an interest to submit comment: http://shop.bsigroup.com/ProductDetail?pid=000000000030358994 Two million people die yearly from work-related incidents and the number of people suffering life altering health conditions caused by their work is exponentially higher. These harrowing figures are in spite of widespread adoption of International Labour Standards, indicating a pressing need for a standard specifically designed to ensure organizations manage the risk and improve their OH&S to protect workers at all levels. ISO 45001 includes the development and implementation of an OH&S policy and objectives which take into account applicable legal requirements and other requirements to which the organization subscribes. The international standard will help provide a single, clear framework for organizations of all types and sizes who wish to improve their OH&S performance and protect those working on their behalf or who may be affected by the organization’s activities. This includes any organization beyond that of sole trader – and those organisations working with multiple contractors, multiple sites, volunteers or temporary staff, etc. Benefits of ISO 45001 include:
Anne Hayes, head of governance and desilience at BSI, oversees the sector which develops health and safety standards and has engaged with BSI’s core markets regarding ISO 45001. She said: “Occupational health and safety is a serious matter for all businesses worldwide, regardless of their size or sector. BSI is proud to be involved with developing a clear framework for businesses wishing to maintain or improve safety within their workplaces. “It is important that ISO 45001 works in alignment with other management system standards, such as ISO 9001 and ISO 14001. Therefore the common text and structure in which ISO 45001 is written will ensure these management system standards are broadly aligned." The international committee which developed ISO 45001 includes experts from over 50 countries and 20 liaison bodies, all with knowledge and practical experience of occupational health and safety issues and the challenges faced. The new standard is based on the core structure and common text developed by ISO for all of its management system standards (MSS), taking into account the requirements of the current OHSAS 18001, other national standards (including those from the US, China and Canada) and the ILO instruments - OH&S guidelines adopted by hundreds of countries across the world. Publication of the final standard is anticipated towards the end of 2017. |
|
|
|
Ian Richardson | 07/03/2017 |
Helping businesses overcome their challenges One of the key parts of my job as a standards publishing manager at BSI (the UK’s National Standards Body) is to make sure we are listening to, and engaging with, our customers and stakeholders with regards to the issues the industry is facing. For health and safety there are numerous ‘hot topics’ which are constantly in the news at the moment... Brexit, EU Directives and Regulations, workplace wellbeing and safety, and even the effectiveness of new world leaders (well, maybe there’s not much a standard can do about that!). But outside of these much talked about subjects and issues, what does the future landscape look like in terms of health and safety? What do you as key players in your industry believe are the main challenges when it comes to conducting your business effectively, successfully and ethically? Is there a product or piece of best practice which you believe would not just help you but also your peers, customers and supply chain? This is where BSI has been instrumental in helping businesses overcome their challenges. Not just by ensuring the UK voice is as strong as it can be when it comes to European and International standards development, but also by helping to produce UK specific documents which get to the market quicker and enable you to respond to emerging needs within your sector. There are currently almost 8,000 standards projects under development and last year there were approximately 5000 comments made on the standards we were developing. What’s vital is that we give you the platform you need to tell us what the next generation of standards should be, and then work with you to create the content. Through organisations such as the BSIF and by working collaboratively with us on ideas, content generation and promotion of the benefits of standards, we stand the greatest chance of UK PLC continuing to go from strength to strength… regardless of what the future may look like. To get in touch, please email me at [email protected] or telephone 0208 996 7721. Ian Richardson, board director, British Safety Industry Federation (BSIF) & standards publishing manager, BSI |
|
|