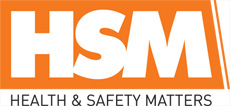
![]() |
Mark Sennett
Managing Editor |
![]() |
Kelly Rose
Editor |
1/2 (1 to 10 of 14)
Sickness absence rates dropping according to survey | 25/04/2018 |
---|---|
EEF, the manufacturers’ organisation, has published the latest Sickness Absence Benchmark, the annual survey of days missed by employees due to sickness in the manufacturing industry. According to the benchmark the overall absence rate dropped in 2017 to 2.2%, down slightly from 2.3% in the previous year.
The average number of days a year lost to sickness absence per employee also declined slightly to 5, down from 5.3 in 2016. At an average of 6.1 days, manual employees lost more than double the number of days to sickness absence than those in non-manual roles, who missed an average of just 3 days a year. The benchmark shows that there is slight variance in days missed across sectors. The rubber, plastics & chemicals sector had the highest average number of days absent at 5.5 and the metals sector the lowest at 4.7 per employee in 2017. There were differences in the number sick days taken between larger and smaller companies too. Smaller companies, with a workforce of up to 50, saw employees each miss on average 3.7 days a year, whereas companies with over 500 employees saw staff miss 7.3 days. Commenting, Terry Woolmer, Head of Health & Safety Policy at EEF, said: “Unplanned leave from staff is something firms look to minimise as it has disruptive and costly consequences for workforce productivity and morale. The small fall in absence rate is therefore a positive sign for the sector. “Whilst staff missing work for sickness is inevitable, gathering as much information as possible and comparing company data to wider trends across the sector is essential for tackling any absence issues before they grow into a larger concern. Today’s data, showing absence rates are slowly declining, indicates that manufacturers are doing just that” |
|
|
|
Manufacturers to tell Government: avoid economic limbo and move quickly to secure Britain’s industrial future | 27/06/2016 |
At a crunch meeting between business groups and the Business Secretary due to take place tomorrow (Tuesday 28th June), EEF, the manufacturers’ organisation, will tell Government that the work to shore up confidence and secure our industrial future is a priority. EEF says it will seek early assurances about the Government’s commitment to securing access to the single market and protecting the UK’s trading relationships. It will also call on the Government to send a clear ‘business as usual’ message to Europe and the rest of the world. At the same time, EEF will urge ministers to avoid allowing business and the UK to fall into limbo by getting on with important investment decisions, such as expanding the UK’s airport capacity. Terry Scuoler, CEO of EEF, also plans to make it clear that the Government has manufacturers’ backing in waiting until the UK has a clear and defined negotiating position before triggering Article 50. He will also reiterate the need to ensure that the migration of workers into the UK is not impaired now or in any future negotiations. Commenting ahead of the meeting, Scuoler said: “The UK Government has a major task ahead of it in supporting growth in the economy and managing the process of securing a new relationship with the EU. In the immediate aftermath of the vote, it must continue to tread carefully by not triggering Article 50 immediately, reassuring the markets and seeking to shore up business confidence. “The next step is clearly for close engagement with business groups and other stakeholders to ensure that emerging signs of manufacturing recovery do not falter in the coming months and to deliver broad agreement on a clear vision for a new relationship between the UK and the EU. "It is vital that Government takes immediate steps to keep manufacturing growth on track – I will be using this meeting to set out the sector’s top priorities in forging a new relationship with partners in the European Union. The collective commitments to make the referendum work for the UK economy are an important first step in offering some stability for business. In mapping out what Government needs to focus on now, both in minimising the short-term risk of economic downturn and setting out the UK negotiating priorities, we must bear in mind the warnings of international organisations that the UK’s manufacturing sector was on the ‘at risk’ list in the event of Brexit.” According to EEF, manufacturers will need to see a re-invigorated Industrial Strategy to anchor large, mobile investors and to support investment and growth in domestic supply chains. A focus on increasing investment, innovation and productivity across the UK industrial sector must now take precedence over deficit reduction. In a statement, the EEF said: "Policies that could support this aim include reinforcing the tax system for capital investment and higher levels of support for research and development through Innovate UK. Decisions on major infrastructure projects should not be further delayed, with critical UK supply chains able to invest with confidence in order to deliver major transport programmes that will support productivity growth in the UK.
The UK needs a deal with the EU that takes account of the specific relationship between the EU and the UK; not a Swiss, Norwegian or even Canadian model, but a UK model. The task ahead of extricating the UK from EU regulation and legislation will be long and complex. Businesses will also require confidence that migration policies will not adversely affect their ability to invest and grow." |
|
|
|
Dame Judith Hackitt set to lead UK’s manufacturing body | 01/02/2016 |
Dame Judith Hackitt, who is stepping down as chair of the Health and Safety Executive at the end of March, has been appointed as chair designate of EEF, the manufacturers’ organisation. She will take up the post on 4 April, replacing Martin Temple CBE, who will step down after more than 17 years as director general and then chairman of the body, which represents manufacturing, and is now in its 120th year. A chemical engineer by profession, Judith Hackitt, who became a Dame in the 2016 New Year Honours, takes the reins of an organisation whose members include a wide cross-section of manufacturers and a sector facing many global headwinds, as it seeks to strengthen manufacturing’s position in a rebalanced UK economy. Her fellow board members, who include representatives from Jaguar Land Rover, Siemens, Tata and the Marshall Group, are preparing for a critical year in which the future of Britain’s role in the EU looms large. |
|
|
|
Powering up health and safety | 19/03/2015 |
Occupational health and safety are core considerations for the electricity generation, transmission and distribution supply industries. Terry Woolmer, head of Health and Safety Policy at EEF, the manufacturers' organisation, examines the issues of public safety and the workforce that maintains and operates the networks. The priority risks for the electricity supply industry include working with electricity, working at height and driving, occupational health as well as public safety issues involving both members of the public (electro-magnetic fields) and third-party contractors. SAFELEC 2010 was a 10 year initiative launched in 1999 which looked at the activities of the electricity supply sector in conjunction with trade unions, contractors and the Health & Safety Executive (HSE). In order to meet Government targets they set out the HSE documents ‘Revitalising Health & Safety’ and ‘Securing Health Together’. SAFELEC reduced the number of working days lost per 100,000 workers through work-related injury and ill health by 30% and cut the rate of fatal and major injury accidents by 10%. Following SAFELEC the electricity supply sector launched a further five year health and safety strategy called ‘Powering Improvement’ which concentrated on the following themes:
The focus for 2015, ‘Working with Contractors’ is concentrating on developing open partnership approaches between electricity supply companies and their contractors in order to share best practice, intelligence and lessons learned in managing common risks such as working at height, working with electricity and occupational ill health. This partnership approach also involves the trade unions at its heart. The idea is that the 2015 focus will lead to openly shared approaches on managing health and safety risks and result in consistent approaches to managing the same H&S risks being shared, promoted and published across the Electricity supply sector. The Electricity Supply industry, together with unions and HSE, subscribe to the following principles developed through its National Health and Safety Advisory Committee (HESAC). They form a key part of the sectors vision and strategy:
One of the obvious risks associated with the industry is working at height. One example includes climbing of overhead line poles, of which there are approximately 4 million poles in the UK, mainly used to support HV and LV overhead lines. A large pole can weigh a quarter of a tonne or considerably more with a transformer or other equipment. The main risks are associated with incorrect erection or decay in service. There have been many incidents where linesmen have climbed decayed poles which have then fallen while the linesmen were on the pole. Some have resulted in serious injuries or fatalities, both to linesmen on the poles and others hit by the falling poles. Direct and contributory causes have included failure to test poles properly before climbing them, climbing poles marked as defective or not changing defective poles. The ‘Powering Improvement’ initiative on Asset management and maintenance led to a modification of Asset Management procedures so that:
|
|
|
|
Industry, government, and professional bodies agree ‘Fit Note’ way forward | 17/12/2013 |
The first sickness absence summit on the Fit Note and long-term sickness absence agrees measures to help return to work. Government, employers, the medical profession and other professional bodies held the first ever summit this month on the Fit Note and long-term sickness absence. Key stakeholders at the summit agreed on a number of measures on how we can make best use of the Fit Note and to reduce unnecessary sickness absence.
EEF, the manufacturers’ organisation had called for a summit earlier in the summer on the back of its annual sickness absence survey of its members, which showed an increasing number of employers believing the Fit Note was not yet resulting in employees making an earlier return to work and that the average duration of long-term sickness absence increasing over the past 5 years, both key factors in promoting economic growth.
The summit featured representatives from 24 organisations including the Department for Work & Pensions (DWP), the British Medical Association (BMA), the Royal College of GPs (RCGP), EEF and the other main stakeholders. It was organised to create a forum for discussion between Government, employers, the medical profession and other professional bodies in order to:
• Secure stakeholder commitments on making best use of the fit note by employers, medical professionals and employees and
• Share novel and innovative solutions to help reduce the length of long-term sickness absence from work
Professor Sayeed Khan, Chief Medical Adviser for EEF said: "Enabling an earlier return to work is a key factor in promoting economic growth. It is important to make the fit note work better for both patients/employees who want to make an earlier return to work. EEF is committed to improving the dialogue between the medical professional and employer. To help this we will develop a templatewhich employees can give to their GP describing the adaptations and modifications their employer can make to facilitate earlier return to work."
Dr Bill Gunnyeon, Chief Medical Adviser for the DWP, said: "Getting the most out of the fit note is a key part of effective sickness absence management - and requires action byemployers, line managers, individuals and doctors. Our substantial programme of research shows that the fit note is starting to have an impactand by early next year almost 100 per cent of GP practices will be able to use the computer-generated fit note. This completes our national rollout programme. Over time we will publish more information on how the fit note is being used to improve our understanding of working age sickness absence. We are also introducing the Health and Work Service to help employees who have been on sickness absence for four weeks to return to work, support employers to better manage sickness absence among their workforce and give GPs access to work-related health support for their patients."
John Chisholm, representing the RCGP, said: "We recognise the need to ensure all GPs are fully engaged with the effective operation of the fit note so that employees are helped to get back to work earlier through the ‘fit for work’ and ‘may be fit for work’ assessment process. The RCGP is committed to the continuation of its national education programme on health and work in general practice. The RCGP will also aim to raise the profile of the fit note by embedding health and work in the continuing education of all GPs including those in training."
John Canning, spokesperson from the BMA said: "We recognise the necessity to make the fit note function more effectively for the patient. There is a recognition by the BMA that ‘good work’ improves both physical and mental health. Our commitment to this process is to help the non GP medical professional understand their part in the fit note process and consider the work element of patients who are discharged from hospital following treatment or who return as outpatients."
|
|
|
|
Government urged to step up efforts to tackle sickness absence as survey shows gains close to exhaustion | 23/01/2013 |
Government is being urged to re-invigorate its efforts to tackle sickness absence and implement the recommendations of the Frost/Black Review as a matter of urgency, amidst new evidence that the long term downward trend in absence rates has plateaued... Government is being urged to re-invigorate its efforts to tackle sickness absence and implement the recommendations of the Frost/Black Review as a matter of urgency, amidst new evidence that the long term downward trend in absence rates has plateaued.
The call was made by EEF, the manufacturers' organisation on the back of publication of the EEF/Westfield Health 2012 annual sickness absence report. The report, which includes the UK's largest private sector business survey of sickness absence, illustrates some continued positive results, especially for those companies taking a proactive approach to managing sickness absence as part of best practice and, who are prepared to work with their GPs to get employees back to work. This approach has resulted in a continued year on year decline in short term absence over the last five years, with one third of companies seeing a decrease in 2011. In addition, the number of employees having no sickness absence has again increased to 51% in 2011, up from 46% in 2010. This reflects the steps that employers have taken in this area, including setting stretching absence targets, training line managers and providing employees with Occupational Health services. Smaller companies continue to have a lower average rate of absence than larger firms. However, despite these efforts the overall sickness absence rate has now flattened off and remained unchanged from 2010 (2.2%), whilst the average working days lost to absence has shown a marginal increase from 5 days per employee to 5.1 days (this still compares to 6.7 in 2007). Of greater concern is the divergence between short and long term absence where almost 40% of companies saw an increase in 2011, an increase of 5% on 2010 alone. This was mainly down to a jump in absence due to stress, anxiety and depression which often result in longer periods off work. In addition, the issue of presenteeism is now being discussed significantly with 55% of companies expressing concerns, in particular on the impact on long term health, short term illness and unmotivated employees. However, only 5% of companies currently monitor the cost of presenteeism. Commenting, EEF chief medical adviser, Professor Sayeed Khan, said: "With our economy still suffering from weak growth we need to pull every possible lever to improve our economic performance. This includes helping employees to return to health and work as soon as possible. There are now signs that the wins to reduce short -term absence are being exhausted and we need a fresh approach from government to address the more deep-rooted problems such as stress and back pain.†"For its part, government must now implement the Frost/Black recommendations as a matter of urgency. In particular it must embed the fit note culture through the training of all doctors and support companies who invest in rehabilitation. At the same time companies should get involved and make the fit note work for them. All the evidence shows the more companies put into the fit note, the more they get out of it." Paul Shires, Westfield Health Executive Director said: “Encouragingly, this year's survey results show a decline in short term absence, particularly amongst those companies which are being proactive in managing sickness absence and are implementing measures such as health insurance. “As the NHS continues to work towards its £20billion savings target by 2014, we would expect the amount of companies taking a more proactive approach to grow, and, it is essential that health insurers continue introducing more relevant benefits to bridge gaps in service provision. However, as the survey shows overall sickness absence has plateaued and stress related absenteeism has grown, it is clear that more needs to be done to aid and assist employers with their healthcare needs.†The survey also shows the continued impact of the 'fit note' two years after its introduction. Whilst 30% of employers say it has made a difference (compared to 11% who find it less helpful), almost 60% of companies say it has made no difference to date. In response, EEF believes that more effort needs to be made to embed this culture if it is to succeed, including the introduction of the electronic fit note as soon as possible in 2012. Furthermore, there should also be increased emphasis on the training of GPs where only 3500 have been trained out of a UK total of over 40,000. However, the positive impact of the training of GPs to date is highlighted by the fact fewer employers see GPs as a barrier to rehabilitation, down to 23% from 34% in 2008. Employers who take a proactive approach to managing sickness absence are also more likely to see the benefits than those who do not. For example those who do not have any barriers to rehabilitation on average have 1.6 days less sickness absence per employee than those who identify barriers. In addition those who proactively contacted their GP about workplace adjustments they could offer their employees were more likely to receive fit notes with 'may be fit for work'. To back proactive companies investing in Occupational Health facilities and rehabilitation, EEF believes government could have a major impact in this area by introducing the tax reliefs recommended in the Frost/Black Review. These would include treatments such as physiotherapy, private medical treatment, health & well- being promotion and healthcare insurance. Other key findings • 13% of companies set 'stretch' sickness absence targets of below 2% with 70% achieving this target • 72% of companies have more than 40% of employees with zero absence, up from 58% in 2010 • Manual workers have a higher absence rate than non-manual (6.7 days per employee compared to 3.2) |
|
|
|
Occupational health services expansion | 23/01/2013 |
EEF, the manufacturers' organisation has announced a partnership with Collingwood Health to increase its range of Occupational Health (OH) services. The partnership will build on the EEF's exisitng experience in the a EEF, the manufacturers'
organisation has announced a
partnership with Collingwood
Health to increase its range of
Occupational Health (OH) services.
The partnership will build on the EEF's exisitng experience in the area. Operating under the existing name of EEF Occupational Health Service, Collingwood Health will expand the service and develop a comprehensive national offering. stress and musculoskeletal disorders. EEF Occupational Health Service has launched a national helpline for help and advice on any OH issues on 0844 800 9264. The service can also be accessed via the website www.eefohs.co.uk. |
|
|
|
New Head of Health & Safety Policy | 23/01/2013 |
EEF, the manufacturers' organisation has appointed Terry Woolmer as its new Head of Health & Safety Policy. In his role Woolmer will be responsible for building on EEF's role as a key stakeholder at UK and European leve EEF, the manufacturers'
organisation has appointed Terry
Woolmer as its new Head of Health
& Safety Policy. In his role Woolmer
will be responsible for building on
EEF's role as a key stakeholder at UK
and European level in the area of
health & safety. As a key strategic
partner of the Health & Safety
Executive he will represent
manufacturers' views and concerns
at UK level, as well as advising on
EEF's role as a major provider of
health & safety consultancy and
training.
He will also represent UK
Employers at European level where
he is currently the sole UK representative
on the European Commission's
Advisory Committee on Safety and
Health (ASCH) working party for
work related musculoskeletal
disorders (WRMSD).
|
|
|
|
Survey suggests ‘Fit note'scheme success | 23/01/2013 |
Sickness absence is continuing on a downward trend amongst UK employees, according to a major survey of sickness absence released by EEF, the manufacturers' organisation, and Westfield Health, one of the UK's leading health insurance providers. Sickness absence is continuing on a downward trend amongst UK employees, according to a major survey of sickness absence released by EEF, the manufacturers' organisation, and Westfield Health, one of the UK's leading health insurance providers.
The EEF/Westfield Health 2011 Sickness Absence Survey shows that from 2007 to 2010 there has been a steady fall in sickness absence, with the average employee taking 5.0 days sickness in 2010 compared to 6.7 days in 2007. Significantly, an all time high of 45% of employees took no days off through sickness in 2010. Whilst recessionary effects may have played a part, this trend began before the recession with year on year improvements over the last five years. The survey is said to show a clear correlation between those companies with strategies in place to train managers in sickness absence and tougher absence targets, with falling absence rates. More than two thirds are now achieving their targets compared to half in 2007 whilst those companies who trained their managers are one third more likely to reduce their sickness absence. Professor Sayeed Khan, EEF chief medical adviser, says: “The continued downward trend in sickness absence is welcome recognition of efforts by companies and government to get people back to work. In particular, it is striking that the companies who have proactively contacted their GPs to discuss adjusting people's working arrangements have seen the highest level of response. |
|
|
|
Health & safety scorecard launched | 23/01/2013 |
EEF, the manufacturers' organisation, has launched a new online tool to help company directors manage health & safety effectively with the minimum of fuss. The tool has been backed by the Health & Safety Executive (HSE). EEF, the manufacturers' organisation, has launched a new online tool to help company directors manage health & safety effectively with the minimum of fuss. The tool has been backed by the Health & Safety Executive (HSE).
The scorecard, sponsored by Travelers, a property and liability insurer, has been developed in response to increasing survey evidence from company boards of the need for pragmatic help in setting and monitoring key performance indicators across their business. The scorecard identifies a mix of measures that reflect a company's performance in the past, and how prepared it is to manage risks and comply with legislation in the future. Straightforward traffic light reporting then enables directors to focus their attention where it is most needed across their business. The scorecard, which is aimed at all organisations not just manufacturing companies, includes step-by-step guidance, worked examples and benchmark statistics as well as a pro forma report that businesses can download and use. Steve Pointer, head of health and safety policy at EEF said: “There is increasing evidence that hardpressed directors need more help with setting meaningful targets and then monitoring them. This means having the right information presented in a rapidly digestible format which will help them make strategic decisions. The scorecard does exactly that and will provide a valuable tool for companies and organisations of all sizes and across all business sectors.†Keith Purvis, general manager, UK for Travelers Insurance Company., added: “Managing health and safety risks in the workplace is a continuous process, and we are delighted to be supporting this initiative and helping companies to better monitor their health and safety performance.†HSE chief executive, Geoffrey Podger commented: “Getting health and safety right in the work place starts with a commitment from those at the top. This tool assists senior management to do it in a straightforward, practical way, helping them set a range of meaningful targets on the key risks the organisation faces and allowing progress to be measured and reviewed. Strong leadership helps the whole organisation maintain a focus on the real health and safety issues, rather then those that are trivial. Explicit, workable targets can also help staff see the important role they play in contributing to a safe workplace." The tool is free to access online at: www.eef.org.uk/scorecard |
|
|